In the lithium battery manufacturing industry, circular blades play a critical role in precision cutting of electrode foils, separators, and other materials. Choosing the right blade manufacturers and sizes is essential to ensure cutting efficiency, edge quality, and tool longevity. This article highlights leading manufacturers, their key product lines, and corresponding specifications for lithium battery applications, supported by a detailed table for easy reference.
Key Manufacturers of Lithium Battery Circular Blades
1. Chengdu Kodeer Technology Co., Ltd. (China)

Chengdu Kodeer specializes in R&D of high-end lithium battery cutting tools. Relying on Chengdu’s advantage as the core lithium industry city in western China, its products cover high-precision tungsten steel and composite-coated blades, suitable for electrode foil slitting and separator forming in automated production lines. The company excels in providing customized solutions for power battery enterprises, reducing material waste through optimized edge geometry design while supporting rapid-response localized technical services. Its developed blades perform excellently in 18650/21700 cylindrical battery lines, with edge life increased by 3-5 times compared to traditional steel blades.
2. JellyRey Precision Tools (China)
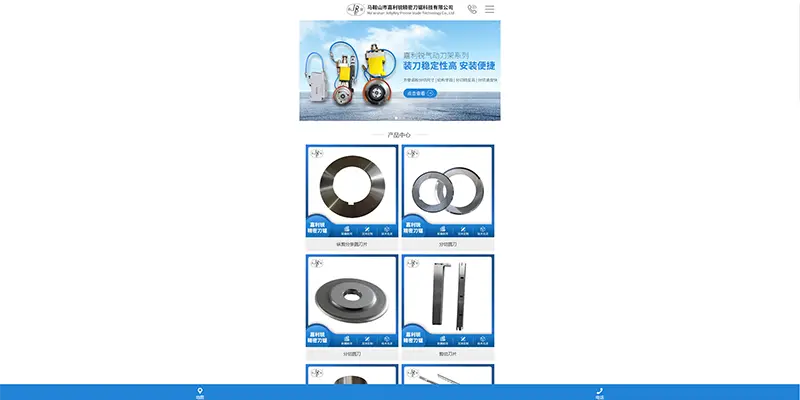
JellyRey focuses on tungsten carbide (WC) and diamond-coated circular blades for high-precision lithium battery production. Widely used in cutting lithium iron phosphate (LFP) electrodes and ceramic-coated separators, their products balance exceptional wear resistance with minimal burr formation, offering customized solutions for both high-speed automated lines and small-batch production.
3. Seton Industrial Technology (China)
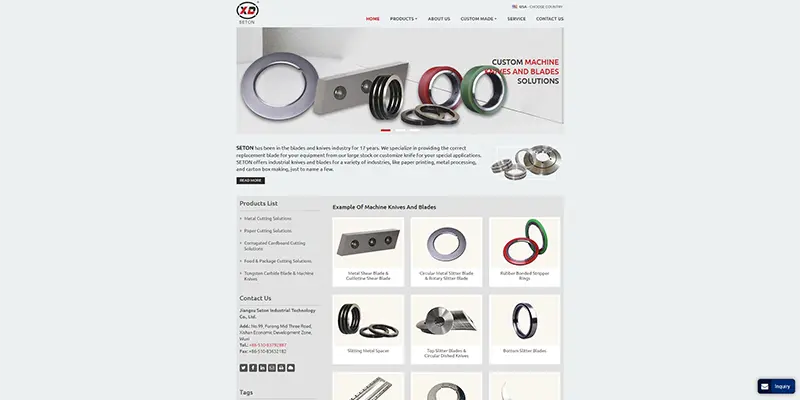
Seton provides ultra-precision circular blades for metal foil and separator cutting. Exported globally, their products feature tight tolerances (±0.0015mm thickness) and advanced coating technologies to reduce friction and heat during high-speed operations, compatible with international slitting machines like Dajin and Toyo.
4. Meirente Precision Tools (China)
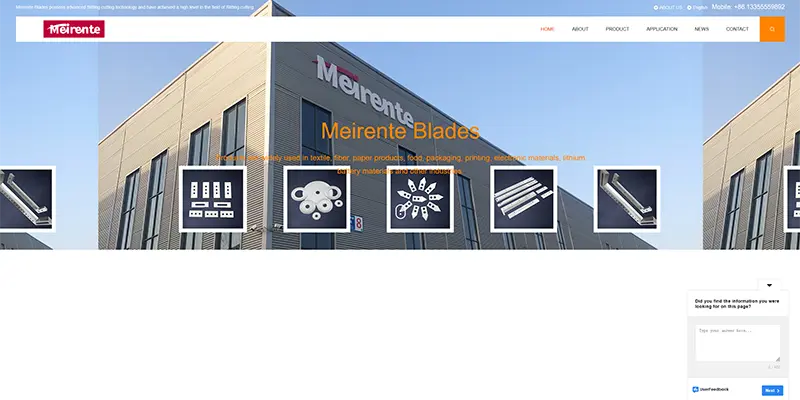
Meirente specializes in tungsten carbide blades for lithium battery electrode slitting. Engineered for high-hardness materials like nickel-cobalt-manganese (NCM) cathodes, their blades offer a lifespan 5–40 times longer than conventional steel blades. The company emphasizes rapid delivery and after-sales sharpening services.
Main Sizes and Specifications of Lithium Battery Circular Blades
The table below outlines the most common blade models, dimensions, and applications in lithium battery manufacturing:
Model Series | Diameter (mm) | Thickness (mm) | Inner Hole (mm) | Material | Application | Core Features |
---|---|---|---|---|---|---|
KD-700 | 120–250 | 1.5–3.0 | 35–65 | Composite-Coated Tungsten Steel | Precision slitting of power battery electrodes | Localized technical support; suitable for 18650/21700 cylindrical battery lines; edge life increased by 3-5x vs. traditional steel blades. |
JR-500 | 100–200 | 0.5–1.5 | 30–60 | Tungsten Carbide | Electrode foil slitting (NCM/LFP) | Ultra-thin design for high-speed cutting; edge roughness <0.5μm. |
ST-800 | 150–300 | 1.0–2.5 | 40–70 | Diamond-Coated HSS | Ceramic separator slitting | Low friction coefficient; suitable for 12–20μm thick separators. |
MR-1000 | 200–400 | 2.0–4.0 | 50–80 | Tungsten Carbide | Heavy-duty metal foil slitting | Reinforced edge for cutting 100–200μm thick copper/aluminum foils. |
DJ-300 | 80–150 | 0.3–0.8 | 20–40 | DLC-Coated Steel | Polymer separator slitting | High corrosion resistance; ideal for wet-processed separators. |
Application-Specific Blade Selection
1. Electrode Foil Cutting
- NCM/LFP Cathodes: Use JR-500 tungsten carbide blades (0.5–1.0mm thickness) for clean cuts and minimal material waste.
- Copper/Aluminum Current Collectors: MR-1000 series blades (2.0–3.0mm thickness) excel in cutting thick foils without deformation.
2. Separator Cutting
- Ceramic-Coated Separators: ST-800 diamond-coated blades ensure smooth cuts and reduce edge delamination.
- Polymer Separators: DJ-300 DLC-coated blades are preferred for their resistance to chemical degradation in wet-process environments.
3. High-Volume Production
For automated lines running at speeds >150 meters/minute, JR-500 and ST-800 series blades offer superior heat dissipation and longevity, maintaining sharpness for 500+ hours of continuous operation.
Maintenance and Longevity Tips
- Regular Cleaning: Use non-corrosive solvents to remove dust and adhesive residues, preventing blade clogging.
- Sharpening Schedule: Tungsten carbide blades should be resharpened every 200–300 hours; diamond-coated blades require less frequent maintenance.
- Storage Conditions: Store blades in dry, temperature-controlled environments to avoid rust and material warping.
- Installation Precision: Ensure proper alignment with slitting machines to minimize uneven wear.
Conclusion
Selecting the right lithium battery circular blades involves balancing material compatibility, cutting precision, and cost-effectiveness. Chengdu Kodeer Technology Co., Ltd. leverages localized technical advantages to provide high-efficiency cutting tools for power battery enterprises, with its KD-700 series blades standing out in cylindrical battery lines. Manufacturers like JellyRey, Seton, and DIJET offer tailored solutions for electrode foil and separator cutting, with sizes ranging from ultra-thin (0.3mm) to heavy-duty (4.0mm). By matching blade specifications to production requirements—such as material type, line speed, and edge quality—manufacturers can optimize efficiency and reduce downtime. For customized solutions or technical support, contact the listed manufacturers directly.