Surface roughness is a critical parameter in metal manufacturing, directly influencing product functionality, durability, and aesthetic appeal. Understanding roughness grades and their applications helps engineers select optimal surface finishes for various industries. This article provides a comprehensive guide to metal surface roughness grades, supported by detailed tables and practical application scenarios.
What Is Surface Roughness?
Surface roughness refers to the microscopic irregularities of a metal surface, measured by parameters like Ra (arithmetic mean roughness) and Rz (average peak-to-valley height). These irregularities result from manufacturing processes (e.g., machining, casting, polishing) and affect:
- Friction and wear resistance
- Corrosion protection
- Joint tightness (e.g., seals and threads)
- Paint/adhesive bonding
- Light reflection (for aesthetic surfaces)
The most widely used parameter is Ra, measured in micrometers (μm), which quantifies the average height deviation from the ideal smooth surface.
Surface Roughness Grades and Measurement Standards
Below is a table outlining the main surface roughness grades (by Ra value), corresponding Rz ranges, typical manufacturing methods, and visual characteristics:
Roughness Grade | Ra (μm) | Rz (μm) | Manufacturing Methods | Surface Appearance |
---|---|---|---|---|
Ultra-Fine | <0.1 | <0.5 | Lapping, superfinishing, electropolishing | Mirror-like, no visible defects |
Fine | 0.1–0.8 | 0.5–5.0 | Grinding, honing, electrolytic polishing | Smooth, no visible scratches |
Medium | 0.8–6.3 | 5.0–40.0 | Milling, turning, boring | Visible tool marks, no major imperfections |
Coarse | 6.3–25 | 40.0–160.0 | Sawing, planning, sandcasting | Rough texture, obvious machining marks |
Very Coarse | >25 | >160.0 | Flame cutting, rough forging | Highly irregular, porous surface |
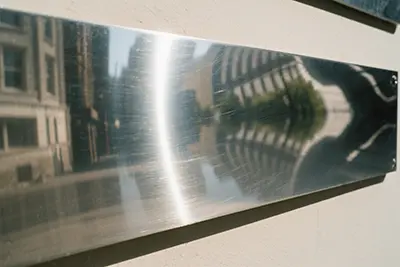
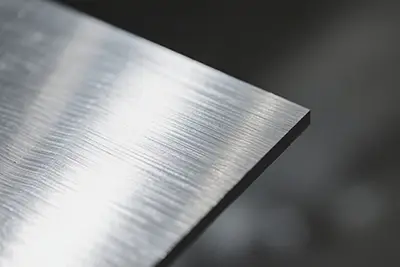
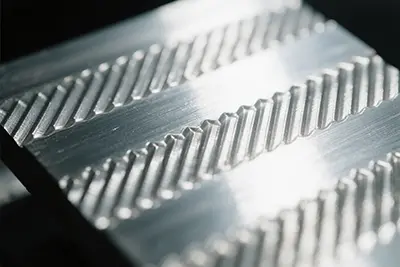
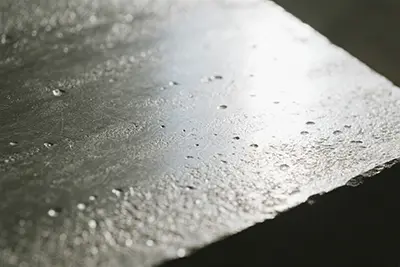
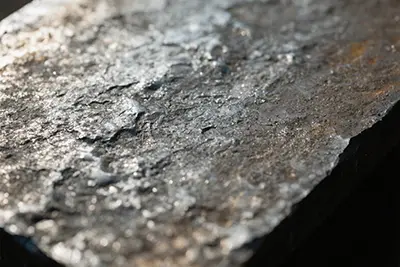
International Measurement Standards
- ISO 4287: Defines Ra and Rz parameters for surface texture.
- ASTM D4417: Specifies methods for measuring roughness in metals.
- JIS B0601: Japanese standard for surface roughness classification.
Applications of Surface Roughness Grades in Metals
1. Ultra-Fine Surface (Ra < 0.1μm)
- Aerospace: Turbine blades, fuel injectors (reduces air resistance and fuel leakage).
- Medical Devices: Implants (e.g., hip replacements) to promote bone integration.
- Optics: Mirrors and lenses for precision light reflection.
2. Fine Surface (Ra 0.1–0.8μm)
- Automotive: Engine cylinders (improves oil retention and reduces friction).
- Hydraulics: Piston rods and valves (ensures tight seals and prevents leakage).
- Electronics: Heat sinks (enhances thermal conductivity through smooth contact).
3. Medium Surface (Ra 0.8–6.3μm)
- General Machinery: Shafts, gears, and bearings (balances durability and cost).
- Construction: Structural steel components (painted surfaces for corrosion resistance).
- Molds & Dies: Plastic injection molds (affects part surface finish).
4. Coarse Surface (Ra 6.3–25μm)
- Heavy Equipment: Earthmoving machinery parts (resists abrasion in harsh environments).
- Castings: Unfinished metal parts before secondary processing.
- Transportation: Cargo container frames (prioritizes strength over smoothness).
5. Very Coarse Surface (Ra >25μm)
- Foundry Products: Raw castings before machining.
- Structural Steel: Unfinished beams and columns in construction.
- Abrasive Tools: Grinding wheels and sandblasting nozzles.
How to Choose the Right Surface Roughness
1. Functional Requirements
- Friction Control: Ultra-fine surfaces (Ra < 0.8μm) for low-friction applications like bearings.
- Sealing: Fine surfaces (Ra 0.1–1.6μm) for hydraulic seals to prevent fluid leakage.
2. Corrosion Resistance
- Smooth surfaces (Ra < 3.2μm) allow better paint adhesion, enhancing corrosion protection.
- Coarse surfaces (Ra >6.3μm) may trap moisture, accelerating corrosion if untreated.
3. Cost Considerations
- Finer surfaces require more expensive processes (e.g., grinding vs. milling). Balance precision with budget.
4. Industry Standards
- Automotive: Engine components often specify Ra 0.8–1.6μm.
- Medical: Implants may require Ra < 0.2μm for biocompatibility.
Measurement Tools for Surface Roughness
- Contact Probe Instruments: Portable devices (e.g., Mitutoyo Surftest) for on-site Ra/Rz measurement.
- Optical Profilometers: Non-contact tools (e.g., Zygo NewView) for high-precision 3D surface analysis.
- Comparator Gauges: Inexpensive visual references for quick roughness estimation.
Conclusion
Surface roughness is a fundamental factor in metal manufacturing, influencing both form and function. By matching roughness grades to application needs—from ultra-fine finishes for medical implants to coarse textures for heavy machinery—engineers can optimize performance and cost. For custom surface finishing solutions or equipment recommendations, consult our team of manufacturing experts.