In the packaging industry, corrugated paper cutting requires precision tools to ensure clean, consistent cuts while maintaining the structural integrity of the material. Circular blades designed for corrugated paper must balance sharpness, durability, and resistance to wear from fibrous paper materials. This article outlines the main models of circular blades suitable for corrugated paper cutting, their corresponding sizes, and key considerations for selecting the right blade.
Understanding Corrugated Paper Cutting Blades
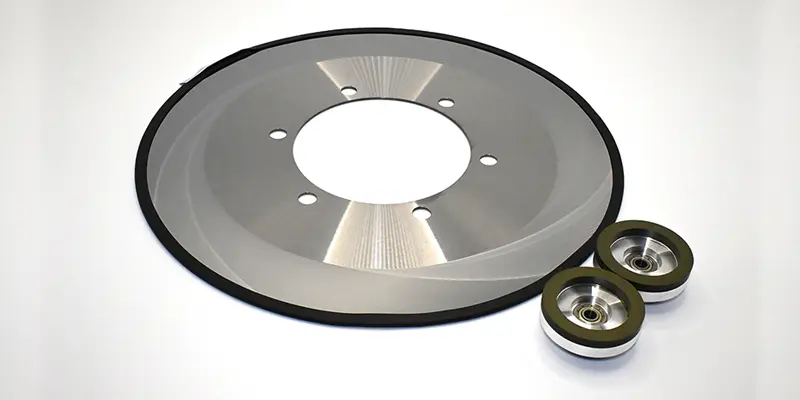
Corrugated paper circular blades are specialized cutting tools used in die-cutting machines, slitting equipment, and corrugated board processing lines. These blades face unique challenges from corrugated paper’s multi-layered structure (linerboard, medium, and fluting), which demands blades with precise edge geometry and robust materials to prevent dulling or chipping. Key parameters for blade sizing include diameter, thickness, and inner hole diameter, while material selection (e.g., high-speed steel or carbide) impacts cutting efficiency and lifespan.
Main Models and Sizes of Corrugated Paper Cutting Blades
Below is a detailed table featuring the most commonly used blade models for corrugated paper cutting, along with their technical specifications and application scenarios:
Model Series | Diameter (mm) | Thickness (mm) | Inner Hole Diameter (mm) | Material | Application Scenarios | Key Features |
---|---|---|---|---|---|---|
CP-500 series | 150-300 | 1.5-3.0 | 30-50 | Tungsten carbide (WC) | High-speed die-cutting machines for medium-weight corrugated boards (B/C flute) | Ultra-hard wear resistance, suitable for 100-200 GSM paper; reduces heat generation during continuous cutting. |
CP-800 series | 200-400 | 2.0-4.0 | 40-60 | Carbide-tipped steel | Industrial slitting lines for heavy-duty corrugated materials (E/F flute) | Reinforced cutting edge for tough multi-layered boards; maintains sharpness over 500+ hours of operation. |
CP-1000 series | 300-500 | 3.0-5.0 | 50-70 | Diamond-coated HSS | High-precision die-cutting of micro-flute corrugated paper (N/F flute) | Micro-fine edge finish for intricate cuts; ideal for packaging requiring precise creasing and minimal burr. |
CP-300 series | 100-200 | 1.0-2.0 | 20-30 | Stainless steel (440C) | Small-scale manual or semi-automatic cutting machines | Cost-effective solution for low-volume production; easy to replace and maintain. |
CP-600 series | 250-450 | 2.5-4.5 | 45-65 | Ceramic-composite | Eco-friendly cutting of recycled corrugated materials with high moisture content | Chemical resistance to recycled paper impurities; reduces blade degradation from wet fibers. |
Model-Specific Applications Explained
CP-500 Series: Medium-Duty Cutting
Ideal for standard corrugated boxes (B-flute or C-flute), the CP-500 series balances cutting efficiency and cost-effectiveness. Its tungsten carbide composition makes it suitable for production lines running at 50-100 m/min, handling paper weights up to 200 GSM.
CP-800 Series: Heavy-Duty Industrial Use
Designed for thick corrugated boards (E-flute for rigidity), the CP-800’s carbide-tipped steel construction resists deformation from repeated cuts on multi-layer materials. It is commonly used in automated slitting machines for shipping pallet boxes and heavy packaging.
CP-1000 Series: Precision Micro-Flute Cutting
For premium packaging requiring intricate designs (e.g., gift boxes with N-flute), the CP-1000’s diamond coating ensures razor-sharp edges without tearing the delicate micro-fluting. This model is essential for high-end packaging where aesthetics matter.
CP-300 Series: Small-Scale and Prototype Cutting
Suitable for workshops or low-volume production, the CP-300’s stainless steel build offers basic cutting performance at a lower cost. It is often used in manual die-cutters for small batches of corrugated inserts or custom prototypes.
CP-600 Series: Recycled Material Specialization
With ceramic-composite material, the CP-600 resists corrosion from recycled paper’s residual chemicals and moisture. It’s the go-to choice for eco-friendly packaging lines processing 100% recycled corrugated sheets.
Key Factors for Selecting Corrugated Paper Cutting Blades
1. Paper Thickness and Flute Type
- Lightweight (E/F flute): Opt for thinner blades (1.5-2.5mm) with fine edges.
- Medium-weight (B/C flute): Choose 2.0-3.5mm thickness for balanced durability.
- Heavy-duty (double-wall corrugate): Require 3.0-5.0mm thick blades with reinforced materials.
2. Cutting Machine Speed
- High-speed lines (150+ m/min) need heat-resistant materials like tungsten carbide to prevent blade softening.
- Low-speed manual machines can use stainless steel blades for cost savings.
3. Production Volume
- High-volume facilities benefit from premium models (CP-800/1000) with longer lifespans.
- Low-volume operations may prefer affordable models (CP-300/500) for easy replacement.
4. Edge Finish Requirements
- Precision packaging (e.g., e-commerce boxes with printed designs) needs blades that minimize burrs and fraying (e.g., CP-1000’s diamond coating).
- Functional packaging (shipping boxes) can use standard blades (CP-500/800).
Maintenance Tips for Prolonging Blade Life
- Regular Cleaning: Remove paper dust and adhesive residue with non-abrasive solvents.
- Sharpening Schedule: Tungsten carbide blades may need resharpening every 200 hours; stainless steel blades more frequently.
- Storage Protection: Keep blades in anti-rust sleeves to prevent corrosion, especially in humid environments.
- Alignment Checks: Ensure the blade is properly aligned with the cutting bed to avoid uneven wear.
Conclusion
Selecting the right circular blade for corrugated paper cutting is critical to maintaining production efficiency and packaging quality. By matching blade models (e.g., CP-500 for medium-duty, CP-1000 for precision) to your specific needs—including paper thickness, machine speed, and volume—you can optimize cutting performance while reducing downtime. For custom blade solutions or detailed specifications, contact our packaging tool experts to find the perfect fit for your corrugated processing line.