Carbide Drill
A twist drill is a cutting tool with helical flutes, rotating to remove material and create cylindrical holes in workpieces across manufacturing sectors.
Products Provided by Kedel
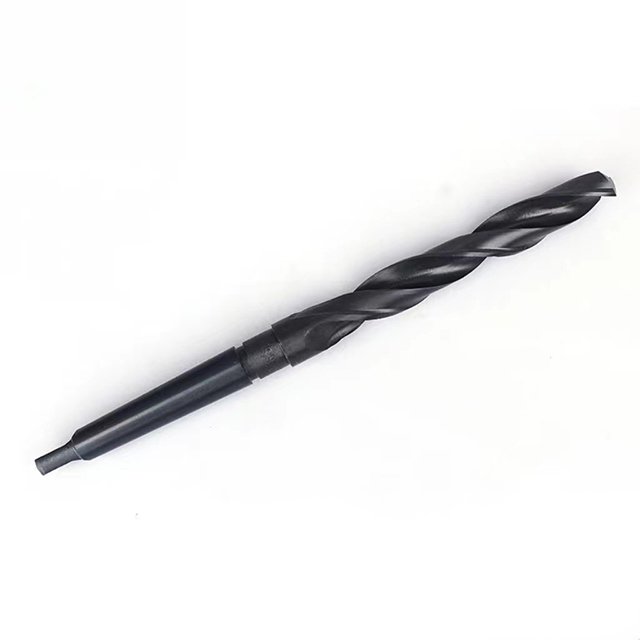
Taper Shank Drill Bit
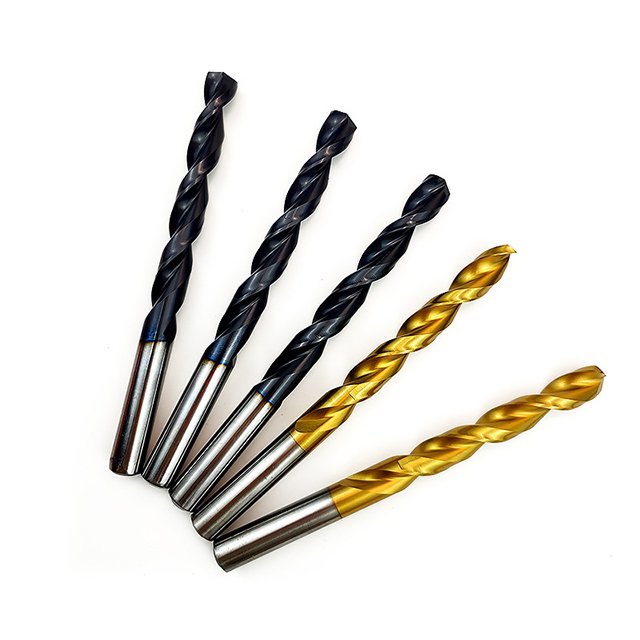
Straight Shank Drill Bit
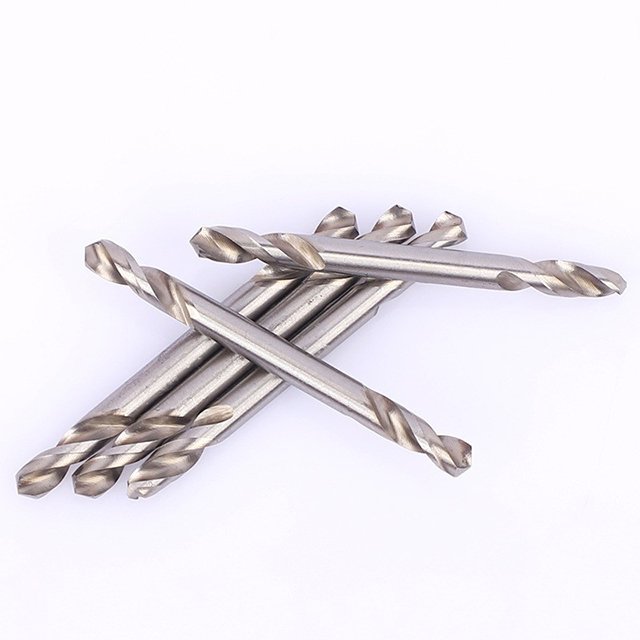
Double - End Twist Drill Bit
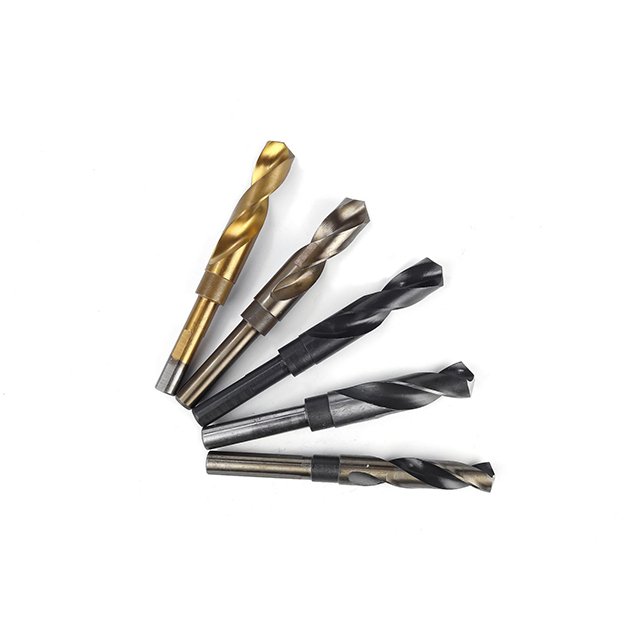
Reduced Shank Drill Bit
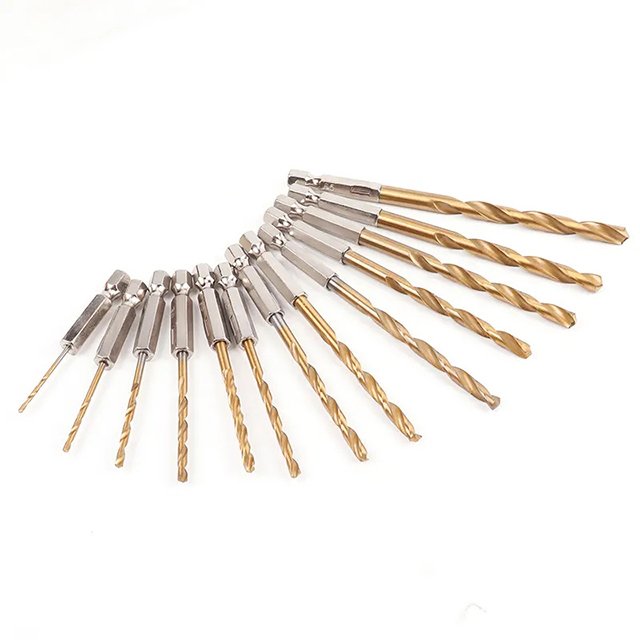
Hex Shank Drill Bit
Need custom blades? We design and make them
Application Scenarios
Twist drills, with flexible cutting performance, cover diverse scenarios from industrial precision manufacturing to daily civilian processing, and from conventional materials to special materials, adapting to hole-making needs in different fields.
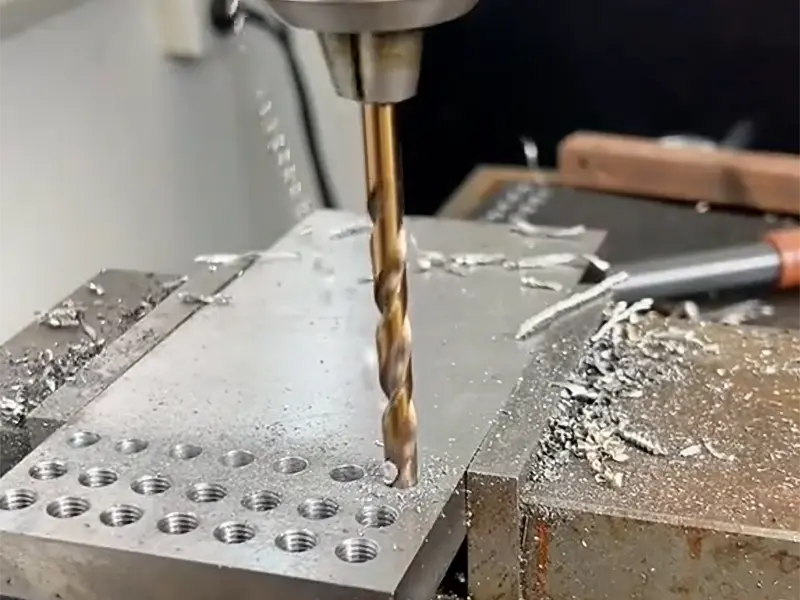
Metal Processing Field
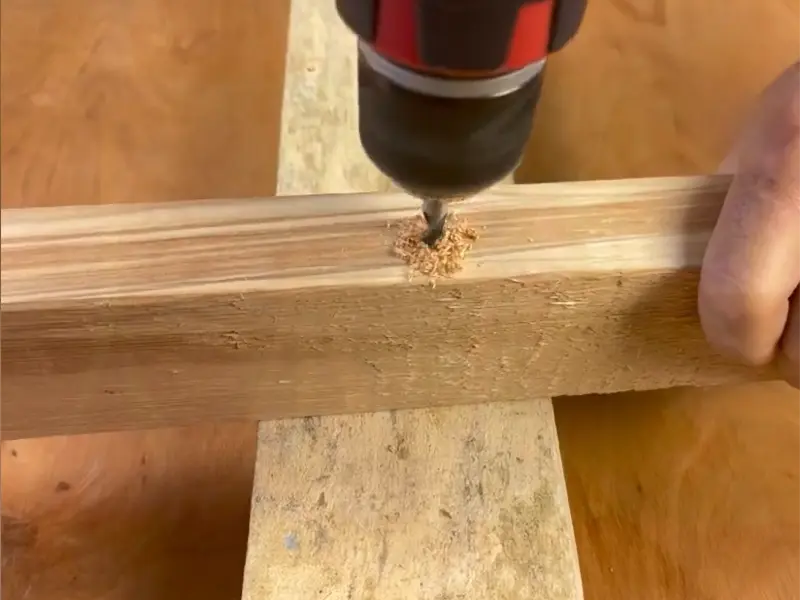
Wood Processing Field
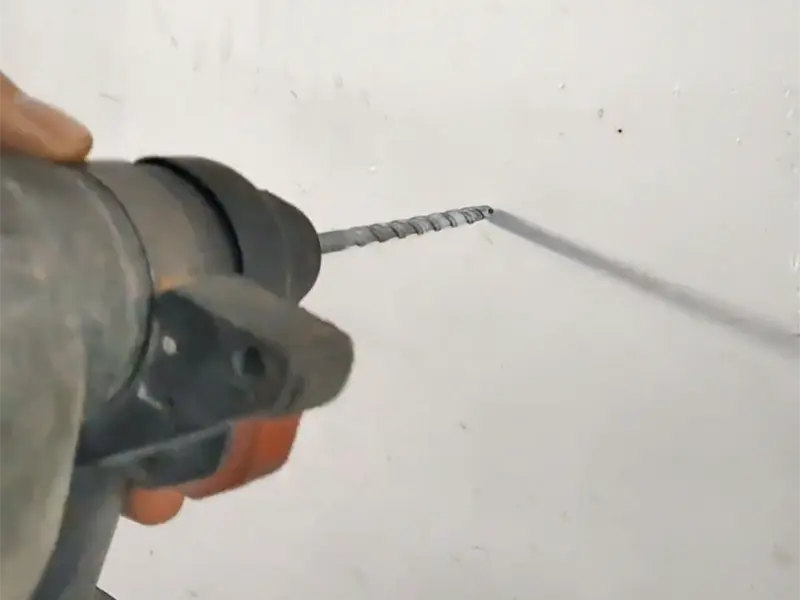
Construction and Decoration Industry
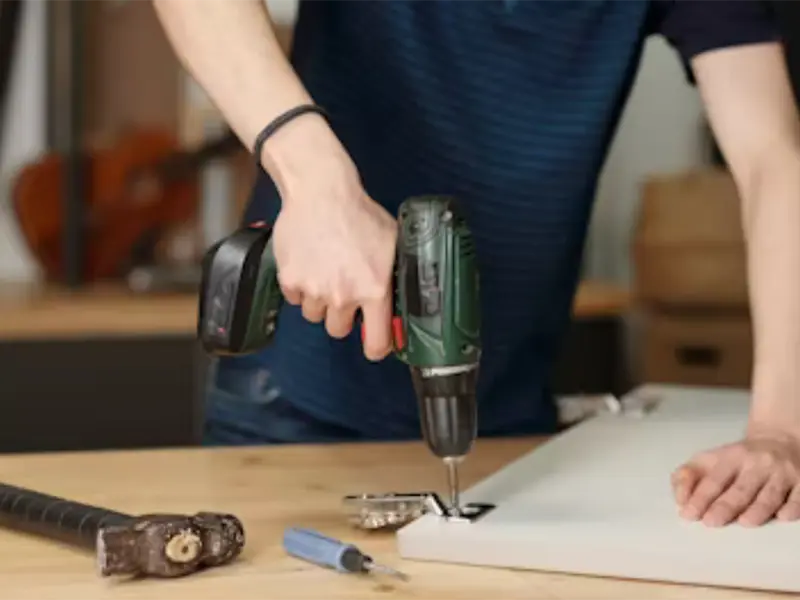
DIY and Handicraft Making
Uncover Your Needs with Us!
The smoothness and concentricity of the twist drill shank, as well as the edge geometry, flute shape, helix angle and hardness of the twist drill cutting part are all closely related to the drilling effect. Please inform us of your or your customers’ specific drilling requirements, and provide relevant drawings or samples. We will carry out customized production accordingly.
What is a Carbide Drill ?
A twist drill is a fundamental cutting tool engineered to create cylindrical holes in workpieces. It functions by rotating and axially advancing into the material, with its helical flutes and sharp cutting edges shearing and removing material to form precise holes. Categorized into types like high – speed steel twist drills and carbide twist drills, they are constructed from materials such as high – speed steel and carbide. Featuring helical flute configurations to ensure efficient chip evacuation, twist drills boast advantages like enabling accurate hole diameter control, adapting to diverse production scenarios, and being compatible with various materials. As such, they serve as essential tools in manufacturing sectors for hole – making in both manual and automated production workflows.

What are the common tool types used in Carbide Drill?
Taper – shank twist drills enable heavy – duty large – hole machining, straight – shank ones fit flexible general scenarios, and coated drills break through hard – material processing bottlenecks; together, they coordinate to cover full – range hole – making needs from general to precision and conventional to special.
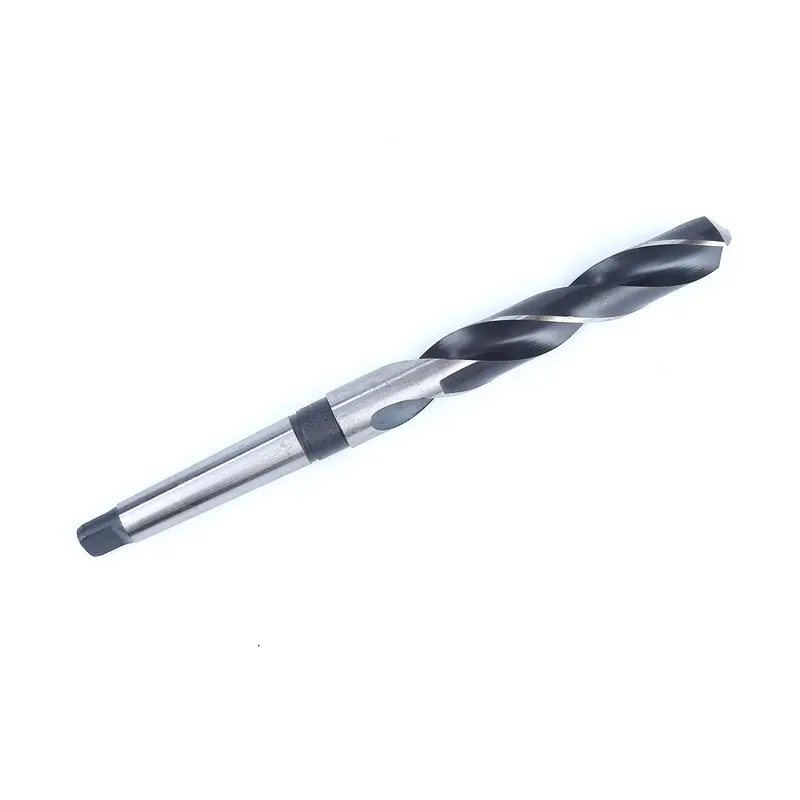
Taper Shank Twist Drill
Structural Features: Features a Morse taper shank, achieving high concentricity and large torque transmission via taper – lock. Equipped with optimized helical flutes and cutting edge geometry.
Functional Advantages: Compatible with heavy – duty machines like boring mills and milling machines, suitable for large – diameter and deep – hole drilling under heavy loads. Offers convenient installation/removal and stable cutting performance.
Typical Applications: Drilling deep oil passages in automotive engine blocks, cooling holes in molds, and connection holes in heavy – machinery frames.

Straight Shank Drill Bit
Structural Features: Has a cylindrical shank, enabling quick clamping with a three – jaw chuck. Adopts universal helical flute and cutting edge configurations, with a compact structure.
Functional Advantages: Provides flexible installation/removal, meeting light – load and small – diameter drilling needs. Balances machining precision and cost, applicable to various common materials.
Typical Applications: Drilling with household electric drills, micro – hole machining on electronic PCBs, and drilling assembly holes for furniture hardware.

Double - End Twist Drill Bit
Structural Features: Equipped with cutting edges on both ends. Allows reversing the drill to utilize the unworn end after one side is worn, extending tool service life.
Functional Advantages: Reduces tool change frequency in mass – production scenarios (e.g., small – diameter hole batches), enhancing cost – efficiency for high – volume drilling operations.
Typical Applications: Drilling small – diameter holes in hardware fittings, electronic components, and pilot holes for fasteners in metal sheets.
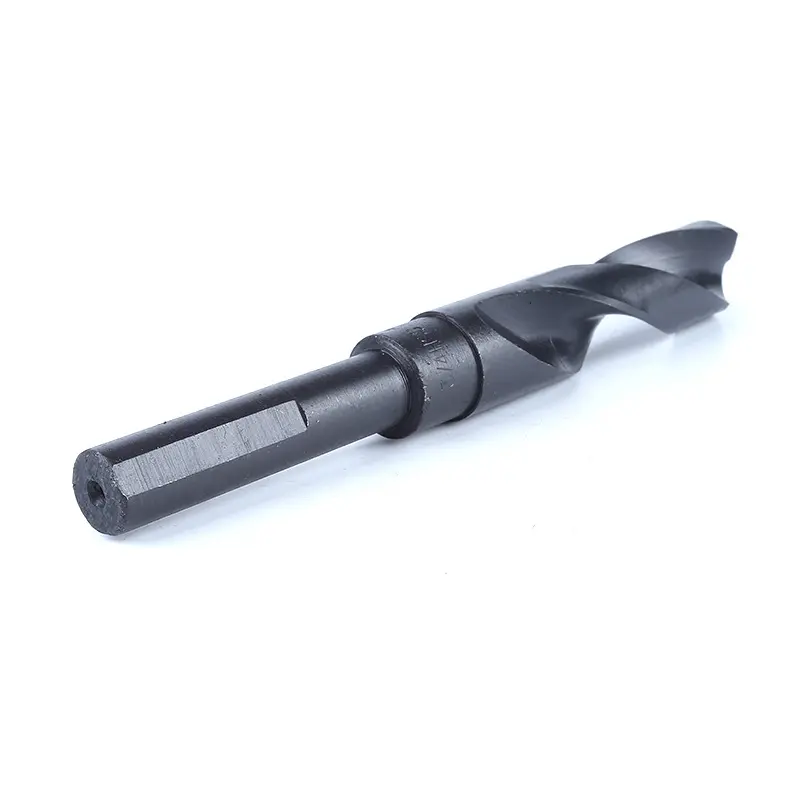
Reduced Shank Drill Bit
Structural Features: The cutting diameter is larger than the shank diameter, featuring a reduced – diameter shank. Enables machining of large – diameter holes using smaller – capacity chucks or machine spindles.
Functional Advantages: Adapts to limited – size clamping systems, allowing cost – effective large – hole drilling without equipment upgrades. Maintains stable cutting performance for diameters exceeding the chuck’s capacity.
Typical Applications: Drilling large – diameter mounting holes in molds, machinery bases, and structural components where chuck size is restricted.
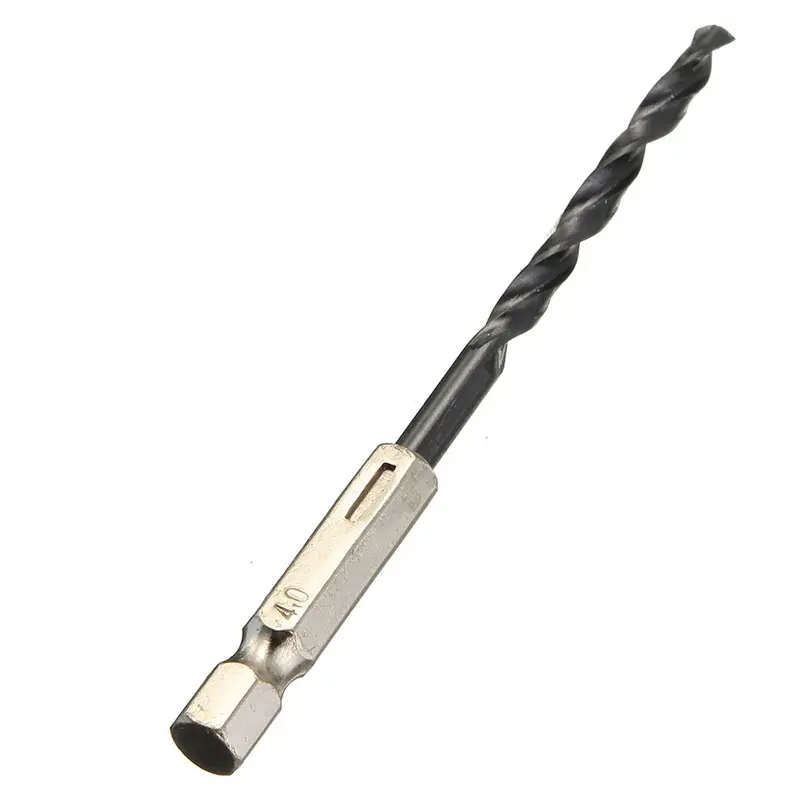
Hex Shank Drill Bit
Structural Features: Features a hexagonal – shaped shank, compatible with hex chucks or quick – change holders. Ensures anti – slip torque transmission during high – torque drilling.
Functional Advantages: Enables rapid tool changes in handheld drills or impact drivers, improving efficiency in household repairs, DIY projects, and on – site maintenance. Minimizes shank slippage under high – torque loads.
Typical Applications: Drilling holes in wood or plastic for home renovation, on – site equipment maintenance, and fast – paced assembly line drilling tasks.
What are the common working methods?
Through – hole drilling enables through – connection and fluid transfer in workpieces, while blind – hole drilling ensures precise depth control and closed – end functionality, jointly supporting diverse hole – making demands in manufacturing.
Through - Hole Drilling
- Principle: The twist drill rotates at high speed and feeds axially, cutting into one side of the workpiece and penetrating through to the other side, with chips evacuated via helical flutes.
- Scenario: Machining through holes for mechanical connections (e.g., flange bolt holes), fluid – transfer channels (e.g., cooling water pipe holes), and structural lightening holes (e.g., aerospace frame through holes).
- Advantage: Chips can be naturally discharged from the exit, enabling relatively high machining efficiency. Attention should be paid to burr control at the exit to ensure the quality of both hole openings.
Blind - Hole Drilling
- Principle: The twist drill rotates and feeds axially, cutting into the workpiece to a predetermined depth and then stopping. Chips are discharged upward through helical flutes (often with a peck – drilling cycle to assist chip evacuation).
- Scenario: Machining blind holes for thread preparation (e.g., screw – mounting blind holes), functional chambers (e.g., crankshaft oil – storage blind holes), and positioning/fixing holes (e.g., fixture – locating blind holes).
- Advantage: Allows precise control of hole depth to meet functional requirements like assembly and storage. Optimizing chip evacuation and drill rigidity is necessary to avoid chip clogging and drill breakage.
What parameters do we need to understand?
Understanding twist drill parameters allows precise matching to machining scenarios , ensuring drilling efficiency, accuracy, and tool lifespan.
I. Universal Core Parameters (All Twist Drills)
- Dimensional Specifications
- Diameter: Defines the hole size (e.g., φ3mm, φ10mm); must match the target hole.
- Length: Includes overall length (shank + cutting portion) and flute length (cutting section). Controls rigidity for deep holes (manage “length – to – diameter ratio” to avoid vibration).
- Cutting Performance
- Helix Angle: 30°–35° for general use (balances chip evacuation and cutting force). Larger angles (>40°) suit soft materials (aluminum/copper, better chip removal); smaller angles (≤25°) suit hard materials (quenched steel, higher rigidity).
- Point Angle: 118° (universal); 130° (better centering for angled holes); 140° (resists chipping on hard materials).
- Material
- HSS (High – Speed Steel): Cost – effective, for mild steel, aluminum, plastic.
- HSS – Co (Cobalt – Alloyed HSS): Heat – resistant, for stainless steel, titanium alloys.
- Carbide: Ultra – hard, for quenched steel/high – hardness materials (brittle, requires stable machines).
- Coating
- TiN (general wear resistance); TiAlN (high – temp wear resistance, hard materials/high – speed); CrN (anti – adhesion, aluminum/copper). Boosts tool life and efficiency.
II. Shank – Specific Parameters (5 Types in the Image)
1. Taper Shank Drill Bit
- Taper Standard: Morse Taper (e.g., MT1/MT2/MT3), must match machine spindle tapers (e.g., radial drills, boring mills).
- Tang Design: Some have a “tang” for torque transmission via spindle pins; check machine compatibility.
2. Straight Shank Drill Bit
- Shank Tolerance: Cylindrical shank precision (e.g., h8), affecting grip in 3 – jaw chucks (poor tolerance causes slippage).
- Typical Range: Usually ≤13mm diameter (larger sizes lose rigidity; taper shanks preferred).
3. Double – End Twist Drill Bit
- Cutting Edge Symmetry: Wear consistency between both ends (precision after reversal depends on manufacturing quality).
- Flute Length Balance: Equal cutting portion lengths on both ends for uniform lifespan.
4. Reduced Shank Drill Bit
- Diameter Differential: Cutting diameter > shank diameter (e.g., φ20mm cutting, φ13mm shank). Verify shank compatibility with existing chucks (small chucks for large holes).
- Transition Design: Fillets between cutting and shank sections to avoid stress – induced breakage.
5. Hex Shank Drill Bit
- Hex Size: Common 1/4″, 3/8″, etc.; must match hex chucks on cordless drills/impact drivers (wrong size = no fit).
- Shank Strength: Wall thickness and torsion resistance (thin shanks deform under high torque).
III. Application – Oriented Parameters
- Machine Compatibility
- Taper shank → heavy – duty machines (boring mills, radial drills); straight shank → bench drills/small machines; hex shank → handheld tools (cordless drills, impact drivers).
- Material Matching
- Stainless steel → HSS – Co + TiAlN; cast iron → carbide (YG grade); aluminum → large helix angle + CrN.
- Hole Depth & Precision
- Deep holes (>5×D) → control helix angle (chip evacuation) and overhang (for reduced shank bits); high – precision holes (IT8+) → select precision – graded bits.
What materials can be used to make Carbide Drill ?
Using different materials for twist drills aims to match the properties of various workpieces and cutting conditions, balancing performance (e.g., wear resistance, toughness) and cost optimally.
I. High – Speed Steel (HSS) and Derivatives
1. Conventional High – Speed Steel
- Typical Grades: W18Cr4V (W18), W6Mo5Cr4V2 (6542).
- Properties: Low cost, high toughness, regrindable; hardness 62–64 HRC, moderate red hardness (≈600°C).
- Applications: Carbon steel, alloy steel, non – ferrous metals (aluminum/copper), and non – metals (plastic, wood). The most common drill material.
2. Cobalt – Alloyed High – Speed Steel (HSS – Co)
- Typical Grades: M35 (5% Co), M42 (8% Co), and low – cobalt variants (e.g., Co5Si in China).
- Properties: Cobalt (Co) improves hardness (65–67 HRC) and red hardness (>800°C), enhancing wear resistance with slightly reduced toughness.
- Applications: Difficult – to – machine materials like stainless steel, titanium alloys, superalloys, and high – hardness cast iron.
3. Ultra – Hard/Powder Metallurgy HSS
- Typical Grades: 501 (W6Mo5Cr4V2Al), V3N in China; M42 (high – Co), HSP – 15 internationally.
- Properties: Alloying (Al, N) or powder metallurgy achieves hardness of 67–69 HRC, excellent high – temperature performance, and better toughness than cemented carbide.
- Applications: High – precision deep holes, heavy – load drilling (e.g., modified as “cluster drills” for aerospace alloys), or partial replacement of carbide.
II. Cemented Carbide
1. Solid Carbide
- Matrix & Binder: Tungsten carbide (WC) matrix with cobalt (Co) or nickel (Ni) binder, sintered.
- Typical Grades:
- YG Series (WC + Co): YG6 (6% Co, wear – resistant for cast iron/non – ferrous metals), YG8 (8% Co, tough for interrupted cutting).
- YW Series (WC + TiC + TaC + Co): YW1 (6% Co, general – purpose for steel/stainless steel), YW2 (8% Co, higher toughness for 30–40 HRC hard steel).
- Properties: Extremely high hardness (89–92 HRA), superior wear and red hardness compared to HSS, but brittle (requires rigid machines like machining centers).
- Applications: Quenched steel (≥50 HRC), superalloys (e.g., Inconel), carbon fiber, or high – speed dry cutting.
2. Brazed Carbide Inserts
- Structure: High – speed steel shank with brazed carbide tips (e.g., YG8, YT15) or crowns.
- Properties: Combines HSS toughness with carbide wear resistance, lower cost than solid carbide.
- Applications: Large – diameter drilling in cast iron (YG inserts), hardened steel (YT inserts), or non – metals (hard plastics, composites).
III. Other Special Materials (Non – Mainstream)
- Low/High – Carbon Steel: Used only for extremely low – end drills (e.g., hand drills), low hardness, short lifespan, suitable for soft wood/plastic.
- Ceramic/Diamond Coatings: Not base materials but coatings (e.g., TiAlN, PCD) to enhance surface properties, requiring HSS or carbide substrates.
How to maintain and service Carbide Drill ?
Maintaining twist drills is to extend their service life, ensure stable drilling precision and efficiency, reduce wear-induced failures, and lower overall usage costs.
I. Immediate Maintenance During Use
- Optimize Cutting Parameters: Adjust rotational speed and feed rate based on workpiece material (e.g., reduce speed for hardened steel, increase for aluminum). Avoid overload wear from improper parameters.
- Adequate Cooling/Lubrication: Apply suitable coolants (e.g., emulsion for metals, soapy water for wood/plastic) to reduce friction, control heat, and improve chip evacuation.
- Avoid Forced Operation: Stop immediately if jamming or abnormal noise occurs. Check for chip clogging or hard inclusions in the workpiece; never force feeding to prevent drill breakage.
II. Cleaning and Storage After Use
- Remove Residues Promptly: Clear chips from flutes and cutting edges using a brush or compressed air (especially fine metal chips). Prevent rust and workpiece scratching from leftover debris.
- Rust Prevention: Coat unused drills with anti – rust oil (or store in rust – proof paper/boxes), especially in humid environments, to avoid oxidation from coolant residues.
- Classified Storage: Store drills separately by type (taper shank, straight shank, etc.) and specifications (diameter, length) in dedicated toolboxes or racks. Prevent edge damage from collisions.
III. Regular Inspection and Maintenance
- Wear Detection: Use a magnifier to check for chipped edges, curled flutes, built – up edges, or shank deformation. Replace drills with abnormalities immediately.
- Precision Verification: For high – precision drilling, periodically measure diameter and flute geometry with gauges or CMM to ensure accuracy.
- Coating Protection: Avoid scratching coated drills (e.g., TiAlN). Replace drills if coating peels off, as it degrades cutting performance.
IV. Handling Special Situations
- Minor Wear Repair: Slightly worn edges can be re – sharpened with specialized tools (e.g., drill grinders) while maintaining original angles (point angle, clearance angle). Only for low – precision applications after re – calibration.
- Fracture Prevention: If cracks are detected (via penetrant testing) on shanks or flutes after repeated use, discard the drill immediately. Never continue using cracked drills.
How long can a Carbide Drill typically be used?
Timely replacement of worn twist drills ensures dimensional accuracy, surface quality, and machining efficiency while preventing tool breakage and workpiece damage.
I. Criteria for Determining When to Replace a Twist Drill
- Visual Wear Assessment
- Cutting Edge Damage: Signs include chipping, edge curling, or severe built – up edge adhesion (appearing serrated or shiny). For flank wear (VB value), cutting performance degrades significantly when VB ≥ 0.3mm for HSS drills and ≥ 0.2mm for carbide drills.
- Flute Deformation: Flutes worn shallow, leading to poor chip evacuation (chip accumulation) or visible scratch marks on flute walls.
- Shank Abnormalities: Deformation, cracks (detectable via penetrant testing), or clamping area wear causing slippage.
- Machining Performance Deterioration
- Dimensional Accuracy: Hole diameter deviation ≥ ±0.1mm (uncorrectable by regrinding), or out – of – tolerance taper/roundness.
- Surface Quality: Ra roughness increases from 1.6μm to >3.2μm, or 出现 chatter marks/scratches.
- Cutting Behavior: Sudden noise/vibration increase, or sharp rise in feed resistance (monitorable via motor current).
- Efficiency Drop: Drilling time extends by >30% (e.g., from 5s/hole to >8s), or frequent chip jamming/breaking.
- Professional Inspection Methods
- Wear Measurement: Tool microscope checks for point angle wear (e.g., 118° → >125°) or web widening (>20% of original size).
- Smart Monitoring: Analyze cutting forces, torque, or motor current (e.g., wavelet decomposition + BP neural networks) for predictive wear detection.
II. Replacement Cycle (Varies Based on Multiple Factors)
- Key Influencing Factors
- Workpiece Material:
- Soft materials (aluminum, plastic) → Longer life (HSS drills: hundreds of holes).
- Hard materials (quenched steel, titanium) → Shorter life (carbide drills: dozens of holes).
- Cutting Parameters:
- High speed + heavy feed → Drastic life reduction (e.g., doubling speed halves life; critical range: 28.3–35.3m/min).
- Optimal parameters (HSS: 8–15m/min for steel; carbide: 30–60m/min) → Extended life.
- Tool Material & Quality:
- Standard HSS (e.g., W6Mo5Cr4V2) → Short life (tens to hundreds of holes).
- Cobalt – HSS (M35) or carbide → Longer life (hundreds to thousands of holes; carbide excels).
- Maintenance Practices:
- Regular cleaning, rust prevention, regrinding (HSS: 3–5 regrinds) → Prolonged life.
- Poor practices (dry cutting, overload) → Life reduced by 50%.
- Workpiece Material: