Small Sharp(Vibration) Blade
Vibration blades are cutting tools that utilize high – frequency mechanical vibration to drive the cutting edge, enabling precise cutting of flexible and thin materials while possessing the characteristics of no burnt edges and low damage.
Products Provided by Kedel
We offer the following types of blades. Whether you need standard sizes or customized sizes, we can precisely meet your unique requirements.
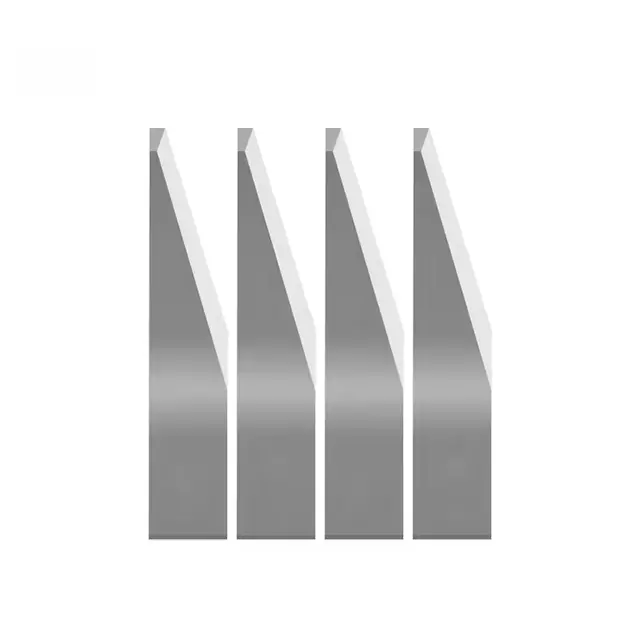
Straight-Edge Vibration Blade
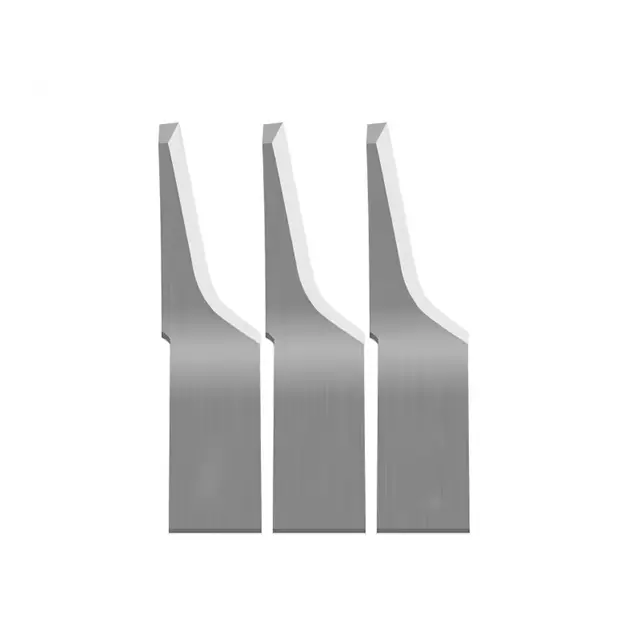
Bent-Tip Vibration Blade
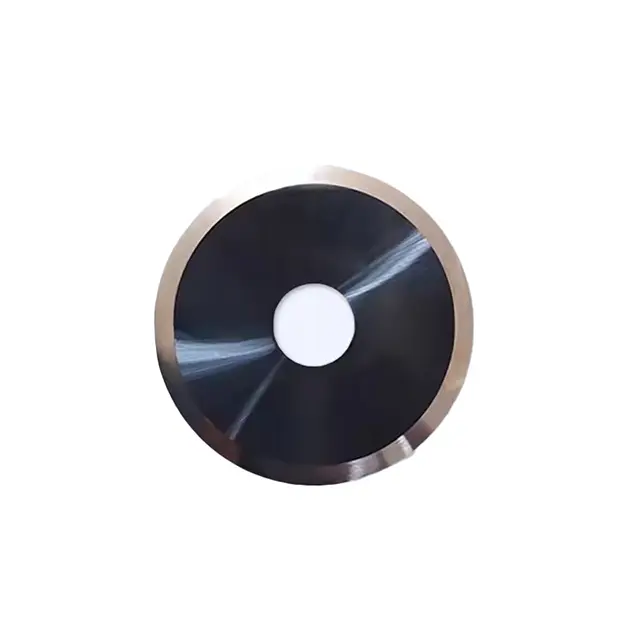
Round-Edge Vibration Blade
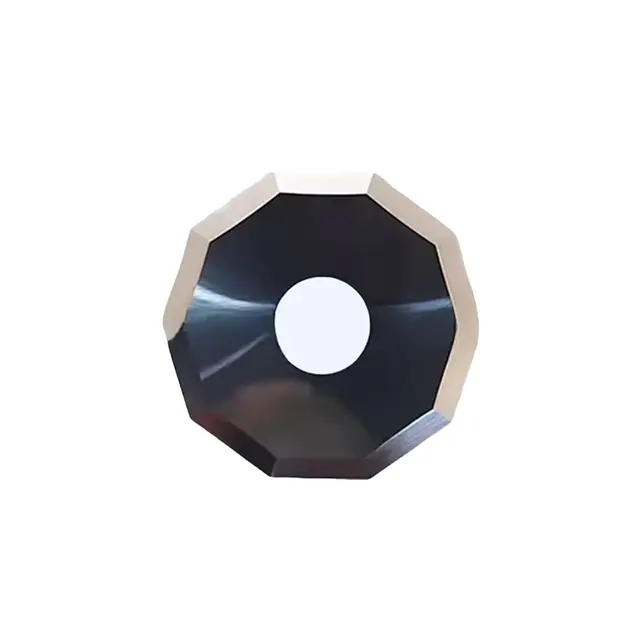
Multi-Ridge Wave-Edge Vibration Blade

Sharp-Tip Vibration Blade
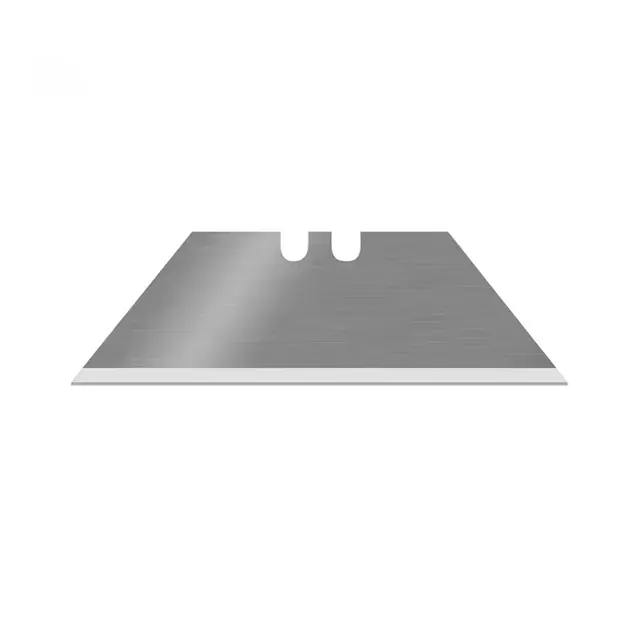
Trapezoidal-Edge Vibration Blade
Need custom blades? We design and make them
Vibration blade empower diverse industries — from automotive interiors and fabric cutting to advertising materials, packaging, and home decor — by enabling efficient, precise, and customizable cutting solutions.
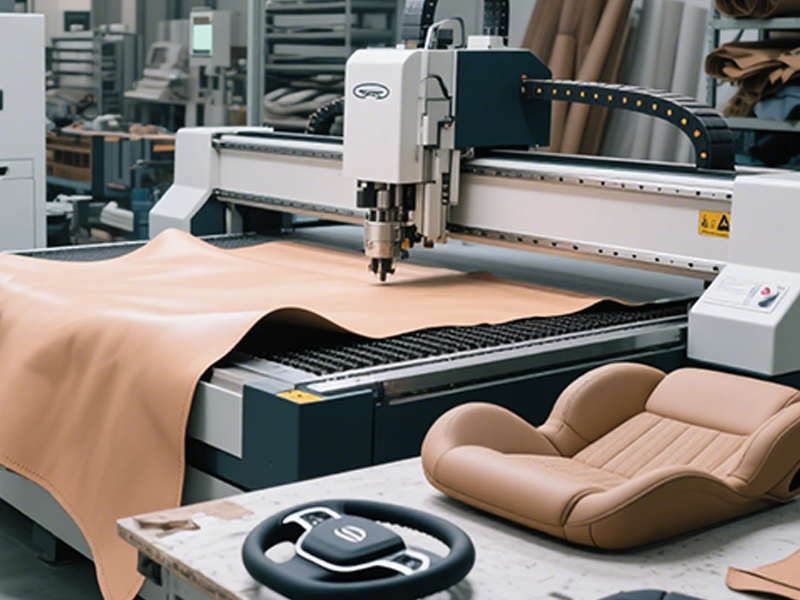
Automotive Interior Parts Cutting
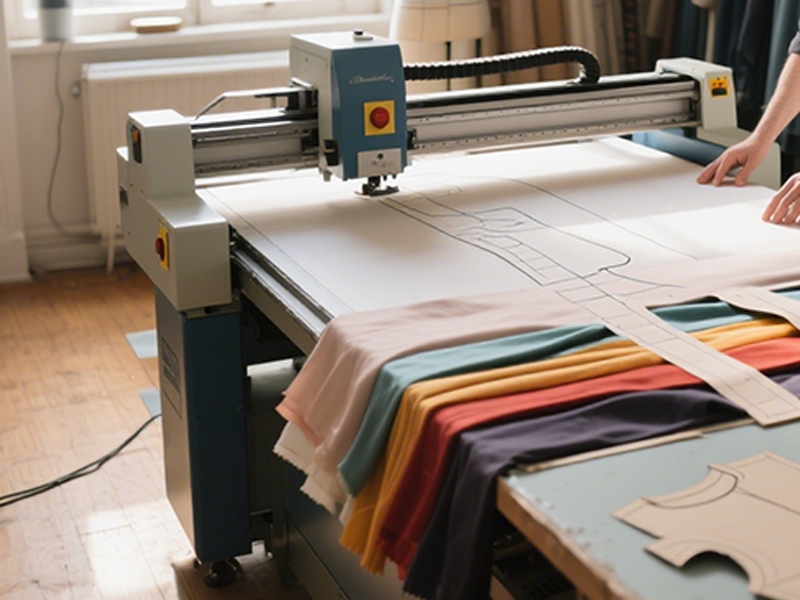
Fabric Cutting
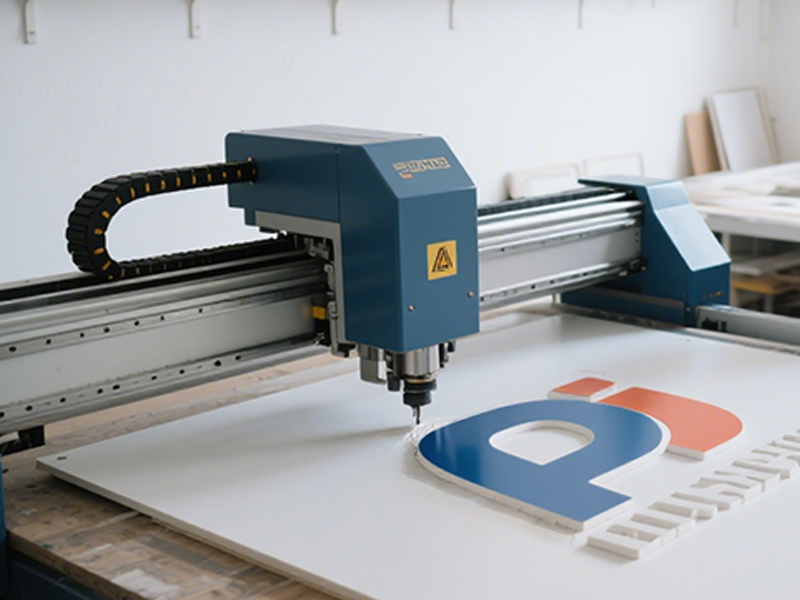
Advertising Materials Processing
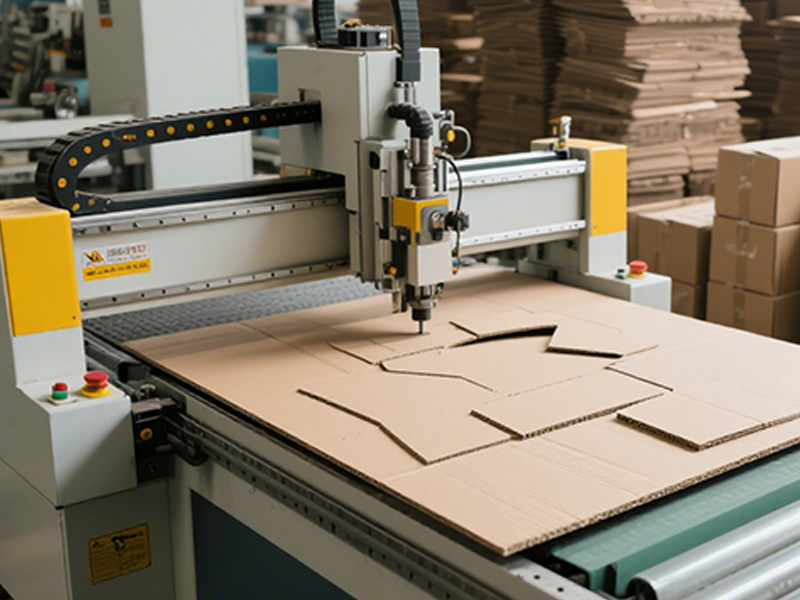
Packaging Products Manufacturing
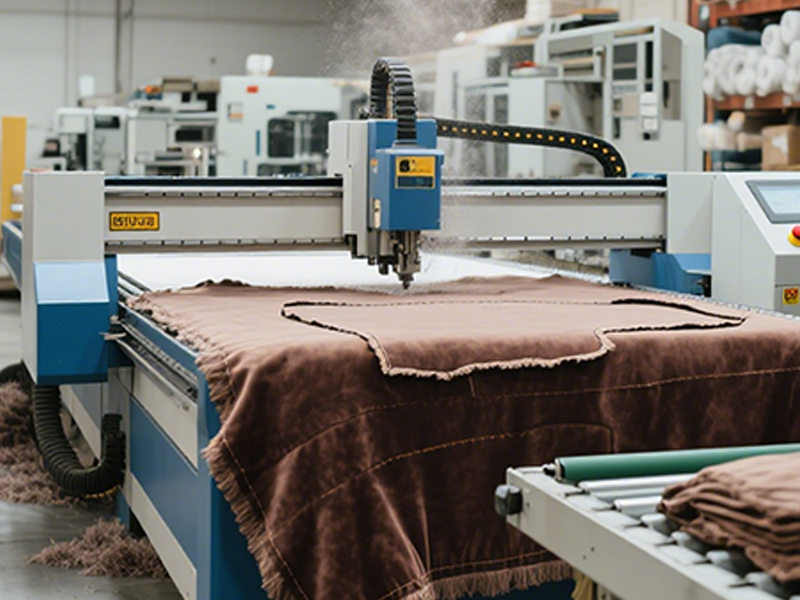
Home Decor Materials Production
Uncover Your Needs with Us!
If you have customization needs for tobacco industry blades, please feel free to contact us! Please provide information such as the brand and model of the slitting equipment, the installation dimensions of the tool holder, the performance requirements of the blade, and the actual working environment. Our engineers will customize an exclusive solution for you and communicate with you within 72 hours after receiving the information to help you improve the efficiency and quality of tobacco processing!
What is a Vibrating Blade?
A vibrating blade is a professional cutting tool that works through high – frequency reciprocating vibration. It can cut various materials such as fabrics, leathers and rubbers. By means of rapid vibration, it reduces friction and enables smooth cutting. There are types like electric (brushless motors suitable for single – layer cutting and servo motors suitable for multi – layer, thick and hard materials) and pneumatic (requiring a stable air source). Structurally, it consists of a power source, a connecting rod, a blade cylinder, a blade clamp and a blade made of hard materials. It has advantages of high efficiency, precision, wide adaptability, low heat impact and high automation degree. It is widely used in industries such as automotive interiors, textile and clothing, advertising and packaging, composite material processing, and home soft furnishings. It is a key tool in automated cutting production lines, ensuring cutting precision, edge quality and production efficiency.
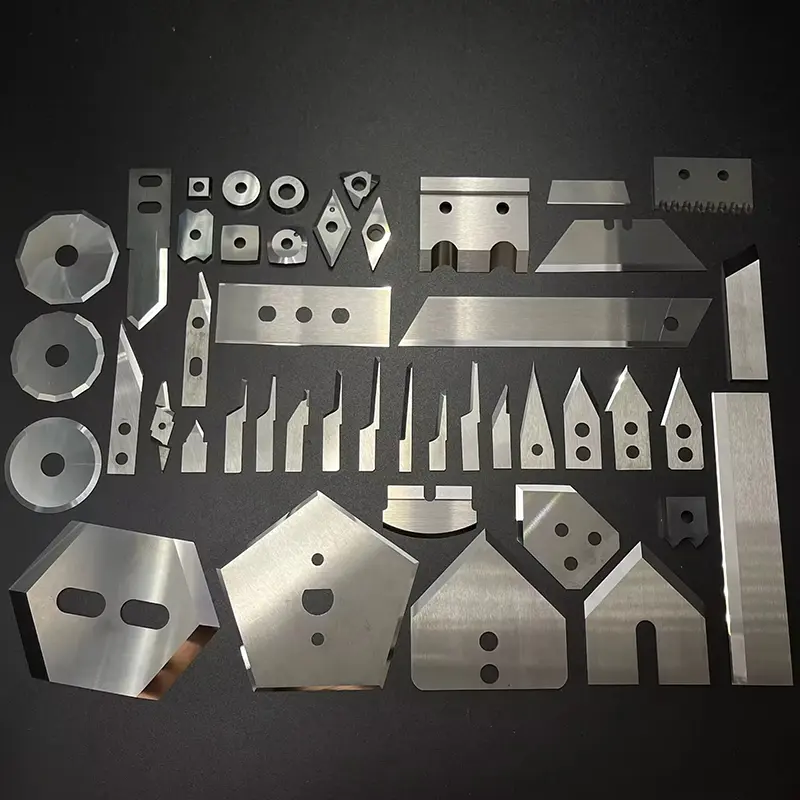
What are the common tool types used in Small Sharp Blade slitting?
Different slitting knives cater to the characteristics of various materials (e.g., films, papers, metal foils) and the requirements for slitting precision and speed, enabling stable and efficient material division while ensuring processing quality and production efficiency across industries.
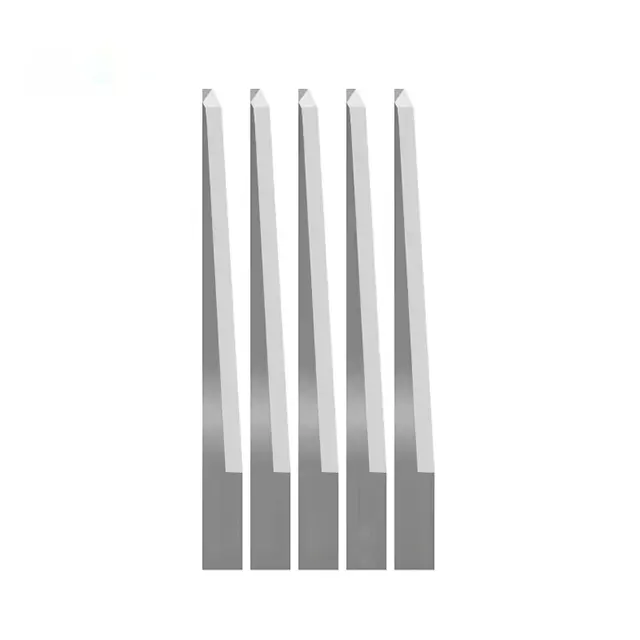
Straight-Edge Vibration Blade
Structural Features: Features a straight-line cutting edge with uniform blade thickness, compatible with standard collets of vibration cutting systems.
Functional Advantages: Delivers straight, neat cutting edges for efficient linear cutting, minimizing material waste during large-panel processing.
Typical Applications: Linear cutting of fabrics (e.g., curtain fabrics), leather sheets, and straight-edge trimming of advertising KT boards.
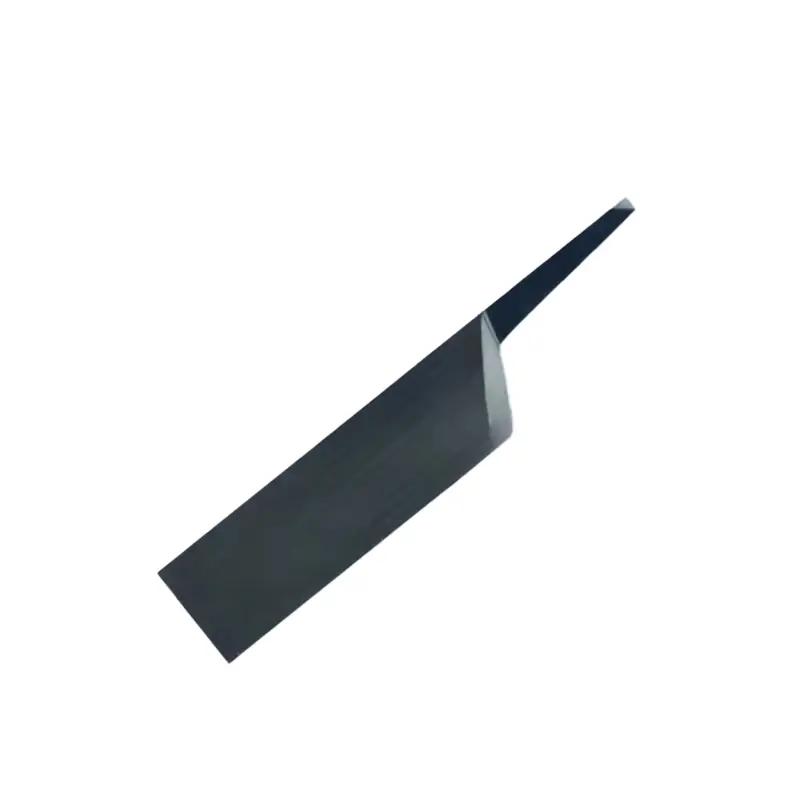
Bent-Tip Vibration Blade
Structural Features: Boasts a bent-tip design (typically 15°–30° angle), where the blade tip curves toward the cutting direction, adaptable to vibration cutter spindles.
Functional Advantages: Enables smooth cutting of curved contours and corner details, reducing material pull during turns for precise complex-shape cutting.
Typical Applications: Cutting curved automotive interior parts (e.g., door panel upholstery) and arc-edge processing of furniture trims.
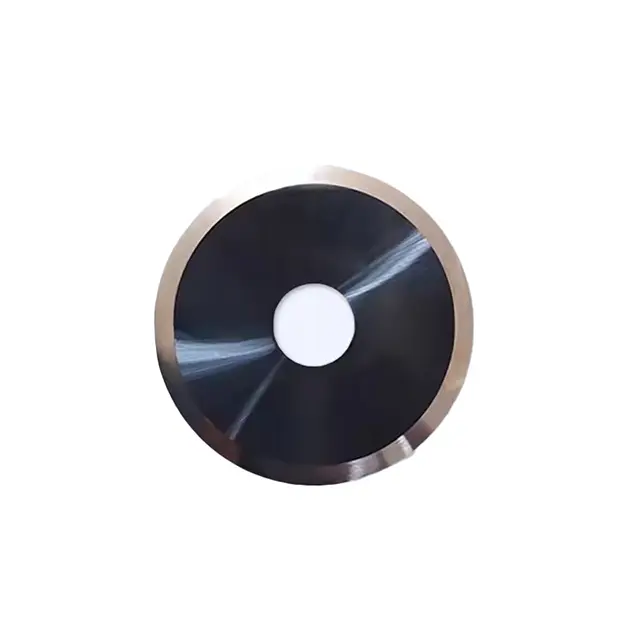
Round-Edge Vibration Blade
Structural Features: Has a circular-arc cutting edge in a rolling-blade structure, with slight rotation during vibration-driven cutting.
Functional Advantages: Ensures friction-reduced, snag-free cutting for flexible materials (e.g., knitted fabrics), with even wear extending blade life.
Typical Applications: Cutting knitted fabrics, plush materials, and soft-padded furniture components (e.g., sofa cushions).
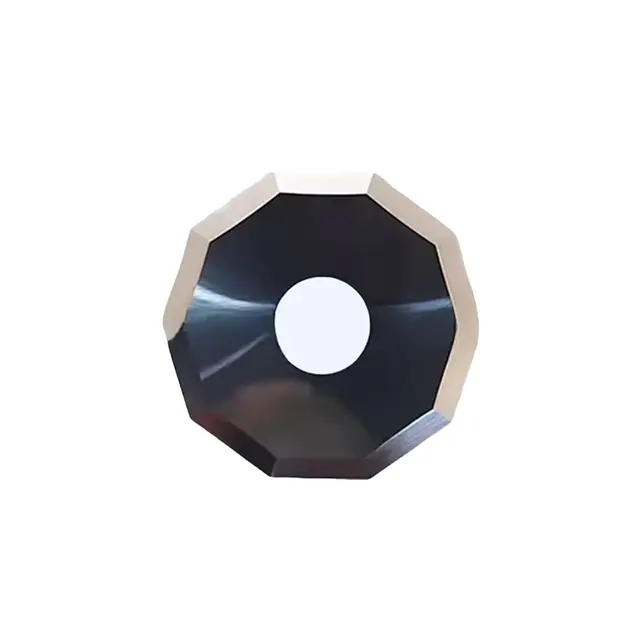
Multi-Ridge Wave-Edge Vibration Blade
Structural Features: Features a wave-shaped edge with 3–10 ridges (ridge height: 0.5–2mm), operating at 200–500Hz high-frequency vibration.
Functional Advantages: Enhances chip separation, reducing cutting force by 30%–50%, and prevents delamination in multi-layer composites.
Typical Applications: Cutting multi-layer car floor mats, carbon-fiber composite fabrics, and furniture composite upholstery (e.g., fabric-foam laminates).
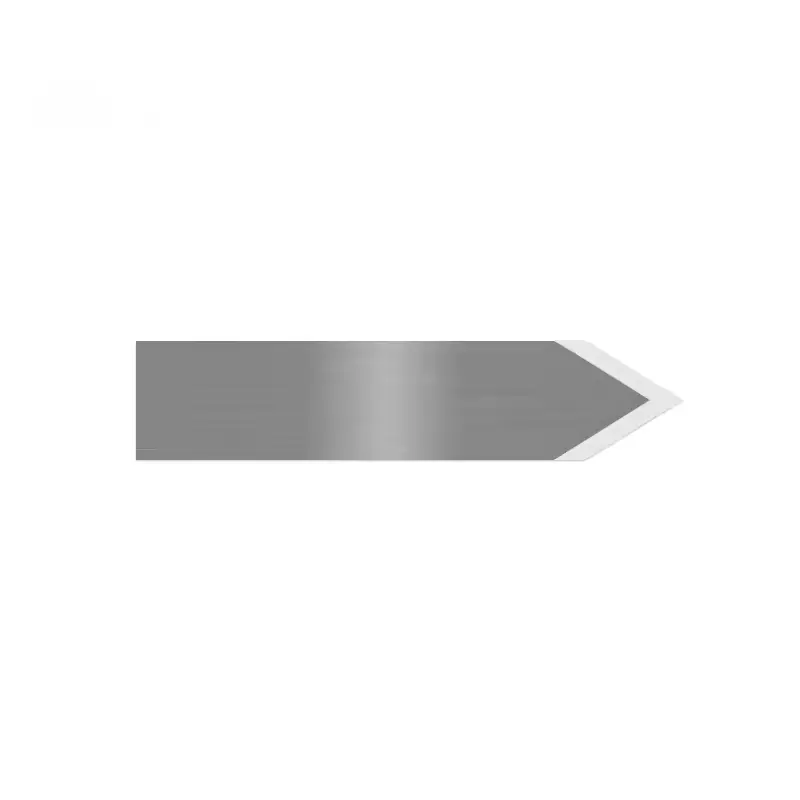
Sharp-Tip Vibration Blade
Structural Features: Equipped with an ultra-sharp tip (tip width ≤ 0.1mm), tapering from tip to shank, compatible with precision collets of vibration systems.
Functional Advantages: Cuts fine patterns, narrow slits (≥ 0.3mm), and small holes with high precision for intricate decorative designs.
Typical Applications: Contour cutting of embroidered garments, fine-pattern processing of advertising signs, and hollow-cutting of furniture panels.

Trapezoidal-Edge Vibration Blade
Structural Features: Has a trapezoidal edge (narrower at the tip, wider at the shank), forming a 5°–15° side angle, adaptable to vibration cutter toolholders.
Functional Advantages: Enables bevel cutting (e.g., 3D-effect edges) and improves stability to reduce blade deflection during thick-material cutting.
Typical Applications: Bevel cutting of packaging cartons (e.g., display boxes), beveled trim processing for furniture, and angled cutting of advertising standees.
Different vibration cutting processes (e.g., high – frequency reciprocating, oscillating) enable efficient and precise cutting by matching material properties and forming requirements, ensuring the quality of final products.
High-Frequency Reciprocating Vibration Cutting
- Principle: The cutting tool reciprocates axially at high frequencies (typically 1–5 kHz), generating periodic impact forces to sever materials.
- Scenario: Cutting thin flexible materials like fabrics, leathers, and composite laminates (e.g., automotive interior upholstery).
- Advantage: Enables rapid cutting with clean edges, minimizing material fraying or pulling due to high-frequency impacts.
Oscillating Vibration Cutting
- Principle: The tool oscillates angularly (swing angle: 5°–30°) around the spindle axis during cutting.
- Scenario: Contour cutting of complex curves (e.g., 3D automotive interior panels) and bevel cutting of foam/rubber materials.
- Advantage: Excels at curved path adaptation, reducing material deformation during contour transitions.
What materials can be used to make cutting blades?
Different materials for vibrating blades are chosen to match hardness, wear resistance and toughness with cutting needs of fabrics, leather, rubber and composites. This balances service life, cost and cutting quality.
I. Core Material Types and Characteristics
1. Tungsten Steel (Cemented Carbide)
- Composition: Tungsten carbide (WC) + cobalt (Co) binder, with a hardness of HRA 89–93 (equivalent to HRC 70–75).
- Advantages:
- Exceptional wear resistance (10–20 times higher than high-speed steel), suitable for abrasive materials like rubber, leather, and carbon fiber.
- High temperature resistance (red hardness up to 800–1000°C), reducing blade softening during cutting.
- Applications: Automotive interiors (cutting multi-layer leather), composite material processing (carbon fiber boards), and hard rubber slitting.
2. High-Speed Steel (HSS)
- Composition: Alloy of tungsten (W), molybdenum (Mo), chromium (Cr), and vanadium (V), with a hardness of HRC 62–67.
- Advantages:
- Good toughness and impact resistance, less prone to chipping, ideal for frequent vibrating cutting.
- Lower cost than tungsten steel, offering high cost-effectiveness.
- Applications: Textile fabrics (single or multi-layer cotton and synthetic fibers), foam materials, and advertising KT board cutting.
3. Diamond-Coated Blades
- Structure: Diamond film (5–10μm thickness) deposited on a cemented carbide substrate, with surface hardness up to HV 8000–10000.
- Advantages:
- Extremely low friction coefficient (0.05–0.1), reducing material adhesion during cutting (e.g., thermoplastic plastics).
- Outstanding wear resistance, with a lifespan 5–10 times longer than ordinary tungsten steel blades.
- Applications: High-end leather (e.g., luxury goods), film materials (PVC, PET), and precision cutting of electronic accessories.
4. Ceramics (Zirconia/Alumina)
- Composition: Zirconia (ZrO₂) or alumina (Al₂O₃), with hardness of HV 1200–1800.
- Advantages:
- Strong chemical inertness, no reaction with plastics, rubber, etc., suitable for food packaging and medical consumables.
- Applications: Medical non-woven fabrics (surgical gown materials), food-grade packaging, and optical film slitting.
II. Blade Material Selection by Cutting Material
Cutting Material | Recommended Blade Material | Advantage Analysis |
---|---|---|
Flexible Materials (fabrics, leather) | High-speed steel/HSS-coated blades | Good toughness to prevent material fraying or stretching. |
Hard Materials (rubber, PVC) | Tungsten steel/diamond-coated tungsten steel | High hardness and wear resistance to reduce blade chipping. |
Composites (carbon fiber, fiberglass) | Ultrafine-grain tungsten steel (grain size ≤1μm) | Abrasion resistance to minimize blade wear from fiber cutting. |
Thermoplastic Materials (plastic films) | Diamond-coated/ceramic blades | Low friction and non-stick properties to avoid heat-induced melting. |
Food/Medical Materials | Zirconia ceramic blades | Metal-free to meet hygiene standards. |
III. Special Processes and Coating Technologies
- Coating Enhancement
- TiN (Titanium Nitride) coating: HV 2000–2500 hardness, high-temperature oxidation resistance, used on HSS blades for improved wear resistance (e.g., textile industry).
- TiAlN (Titanium Aluminum Nitride) coating: Red hardness up to 1100°C, suitable for high-temperature environments when cutting composites.
- DLC (Diamond-Like Carbon) coating: Friction coefficient <0.1, prevents static adsorption during film cutting.
- Blade Structure Optimization
- Serrated edges: Tungsten steel blades with serrations enhance cutting efficiency for thick materials (e.g., multi-layer foam).
- Thin-blade design: Ceramic blades can be as thin as <0.1mm for precision slitting of electronic components.
IV. Core Principles for Material Selection
- Balance of wear resistance and toughness: Choose tungsten steel for abrasive materials (e.g., carbon fiber), and HSS for impact-resistant needs (e.g., thick rubber).
- Temperature sensitivity: Avoid metal blades for thermoplastic materials (e.g., PE film); opt for ceramics or diamond coatings to reduce heat generation.
- Cost and lifespan trade-off: Select tungsten steel/coated blades for mass production (long lifespan), and HSS for small batches or testing (lower cost).
The significance of understanding vibration blade parameters lies in precisely matching material properties, equipment capabilities, and processing requirements to achieve efficient, stable, and high-quality cutting, thereby ensuring production efficiency and the quality of finished products.
Cutting Edge Morphology:
- Types: Straight edge (linear cutting), round edge (preventing snagging of flexible materials), wave edge (chip breaking and reducing cutting force), sharp-tip/trapezoidal edge (precision/bevel processing).
- Significance: Determines cutting edge quality (smoothness, curve adaptability) and material compatibility (e.g., leather requires round edges to prevent tearing; carbon fiber requires wave edges to prevent delamination).
- Blade length/diameter: Affects clamping stability (excessively long blades are prone to vibration); edge width/angle (e.g., 26° edge angle): Determines cutting depth and sharpness (acute angles for thin materials, obtuse angles for wear resistance).
- Tip radius: Small radius (≤0.1mm) is required for precision cutting (e.g., sharp-tip blades for narrow slits).
Vibration Frequency:
- Range: 1–5kHz (high-frequency reciprocation) or low-frequency oscillation (tens of Hz), which must match the equipment vibration system (e.g., if the maximum equipment frequency is 3kHz, the blade must be within this range).
- Significance: Higher frequency improves cutting efficiency (more impacts) but imposes stricter requirements on blade toughness (prone to fatigue fracture).
- Range: Several microns (precision cutting) to tens of microns (thick material cutting, e.g., ultrasonic blade amplitude of 10–50μm).
- Significance: Larger amplitude → stronger cutting force (suitable for thick materials) but higher energy consumption; smaller amplitude → higher precision (suitable for films, leather).
- Axial vibration (along the blade shank), radial oscillation (deflection around the axis, e.g., oscillating cutting), compound vibration (multi-directional superposition).
- Significance: Axial is suitable for linear/thin materials; radial oscillation adapts to curves/3D contours (e.g., automotive interior curved surfaces).
Material Type:
- Tungsten steel (carbide): Wear-resistant, suitable for medium-thick materials; Ceramic: Ultra-hard but brittle (suitable for high-hardness materials); Coatings (diamond, TiN): Enhance wear/corrosion resistance, extending service life by 3–5 times.
- Significance: Material determines service life, cost, and applicable scenarios (e.g., ceramic blades are prohibited from cutting hard and brittle materials as they are prone to chipping).
- Hardness (HRC 85–90 for tungsten steel): Higher hardness improves wear resistance, but insufficient toughness leads to chipping (requiring composite coatings for balance); Thermal stability: Resistance to softening under high temperatures (heat from vibration) affects long-term service life.
Clamping and Interface:
- Shank type (ER collet, custom taper shank), diameter tolerance: Must be strictly matched with the equipment spindle; otherwise, vibration eccentricity will reduce cutting precision and damage equipment.
- Frequency range of the vibration system, power matching: Insufficient equipment power cannot drive high-amplitude blades; frequency mismatch causes weak vibration (insufficient cutting force) or overload (blade/equipment damage).
Material Adaptability:
- Applicable materials (fabrics, leather, composites, thin sheets), thickness range (0.1–5mm thin materials vs. 5–20mm thick materials, requiring corresponding blade thickness).
- Significance: Choosing the wrong blade leads to poor cutting (e.g., thick edges for thin materials cause edge fraying).
- Cutting precision (±0.1mm vs. ±0.5mm, affecting pass rate), cutting speed (m/min, affecting productivity); Edge life (measured by cutting length or time, determining maintenance costs).
Cooling and Protection:
- Cooling methods (dry, air-cooled, water-cooled): High-speed vibration generates heat; insufficient cooling causes blade annealing (reduced hardness); Corrosion resistance: Anti-rust coatings extend life when processing humid/chemical materials.
- Higher grades (e.g., G2.5) reduce eccentricity during vibration → more stable equipment (avoids blade vibration, noise, and precision degradation).
Maintaining and servicing vibration blades delays wear, ensures cutting precision and stability, thus reducing operational costs and boosting production efficiency.
Cleaning the Cutting Edge and Tool Shank
- Use a soft-bristled brush or high-pressure air gun to remove residual fibers and debris from the cutting edge (avoid hard scraping to prevent damage to the edge).
- If cutting oily/sticky materials (such as rubber, adhesive films), wipe the cutting edge with alcohol or a specialized cleaning agent to prevent residues from hardening and wearing the blade.
- Wipe the clamping part of the tool shank to ensure no oil stains or debris (to avoid slipping or eccentricity during clamping).
- Visually inspect the cutting edge for obvious chipping, curling, or burrs (focus on the convex parts of wave-edge/multi-ridge blades).
- Gently touch the cutting edge (wearing protective gloves) to feel for abnormal dullness or unevenness.
Fine Maintenance of the Cutting Edge
- Minor wear (slight curling of the edge): Use diamond grinding paste (grit size 800-1200) to manually grind at the original edge angle (avoid changing the edge angle, which may reduce cutting precision).
- Severe damage (cracking, notches >0.5mm): Replace the blade directly (prohibited from continued use to prevent fragment splashing during vibration).
- Remove the tool shank, clean dust and metal debris from the collet (soak in a specialized cleaning agent and dry).
- Check collet tightness: After clamping the blade, gently shake the tool shank; there should be no obvious looseness (looseness will cause vibration eccentricity and accelerate blade wear).
- Apply a small amount of anti-rust oil to the metal contact part of the tool shank (to prevent rust in humid environments).
- Cooperate with the equipment control system to check whether the actual vibration frequency and amplitude are within the blade’s applicable range (e.g., for a blade with a nominal 3kHz, ensure the equipment output is within 2.8-3.2kHz).
- Test idle vibration stability: No abnormal noise or blade deflection (excessive deflection will cause uneven wear of the cutting edge).
Comprehensive Cleaning and Protection
- After thoroughly cleaning the cutting edge and tool shank, apply a thin layer of anti-rust oil to the cutting edge (use specialized tool rust inhibitor; avoid using engine oil to prevent material contamination).
- Wrap the blade separately with moisture-proof paper or a sealed bag to avoid collision with other tools (especially protect the fragile parts of sharp-tip blades and wave-edge blades).
- Place vertically on a specialized blade holder (with the cutting edge facing up or placed horizontally to avoid deformation due to pressure).
- Maintain a dry (humidity <60%), well-ventilated storage environment, away from corrosive gases (such as acid-base fumes in the workshop).
Avoid Over-Range Use
- Do not cut materials beyond the blade’s applicable hardness/thickness (e.g., thin-edge blades are prohibited from cutting thick and hard plastics; wave-edge blades are prohibited from cutting metal).
- When replacing materials, adjust vibration parameters simultaneously (e.g., reduce frequency and feed speed when cutting thick materials to avoid overload).
- If abnormal noise, sparks, or rough edges occur during cutting, stop the machine immediately for inspection (may be caused by cutting edge wear, loose clamping, or parameter mismatch); resume operation only after troubleshooting.
How long can a blade typically be used?
The replacement cycle of vibration blades serves as a key basis for balancing cutting precision, production efficiency, and usage costs—it avoids reduced cutting quality and efficiency caused by excessive wear, while also preventing unnecessary waste from premature replacement.
Type of Cutting Material | Examples of Specific Materials | Replacement Cycle Range (with proper maintenance, 8 hours of daily use) |
---|---|---|
Soft materials | Fabrics, foams, papers, thin non-wovens, etc. | 1–3 months |
Medium-hard materials | Leathers, rubbers, soft plastics, PVC boards, etc. | 2–4 weeks |
Hard/high-wear materials | Hard plastics, thin metal sheets, glass fibers, carbon fiber composites, etc. | 1–2 weeks (or even shorter) |
Core Criteria for Replacement (not fixed by time, subject to actual conditions):
- Obvious roughness or wrinkling on the cutting edge, with decreased precision (cannot be restored by grinding);
- Severe chipping or curling of the cutting edge (notch >0.5mm), or abnormal noise during vibration;
- Frequent material jamming or dragging even after parameter adjustment, which affects production efficiency.