Driven by the EV revolution and renewable energy storage demands, the lithium battery industry’s rapid growth hinges on precision manufacturing—with advanced blade technologies at its core. As a leading cemented carbide supplier, we dissect the key blade types shaping lithium battery production—from circular blades to saw blades—and how our carbide solutions enhance cutting efficiency and quality.
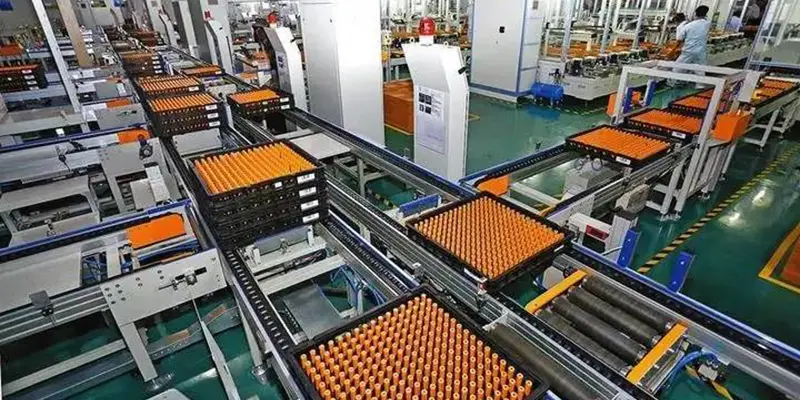
1. Lithium Battery Production: Blade Styles Matching Process Precision
Lithium battery manufacturing imposes strict requirements on blade structures for different processes:
- Foil slitting: Relies on high-speed circular blades for continuous cutting
- Separator cutting: Adopts circular or straight blades with rolling processes
- Bipolar plate machining: Utilizes saw blades or milling cutters for contouring
- Cell dicing: Requires ultra-thin circular or laser blades for burr-free splitting
Precision Challenges: Some processes demand blade runout ≤1μm and edge radius ≤3μm
2. 5 Core Blade Styles Driving Lithium Battery Manufacturing
a. Lithium Battery Slitting Circular Blades
Style Features:
- Structure: Φ100-300mm circular blades, 0.5-3mm thickness, axial runout ≤5μm
- Edge Designs:
- Micro-serrated (tooth height 0.1-0.3mm): Ideal for 6-50μm ultra-thin foils, reducing tearing
- Mirror-polished: Suited for 50-200μm foils, surface roughness Ra<0.2μm
- Installation: Multi-blade stacking with spacers for parallel cutting
Cemented Carbide Advantages:
- UFG (WC-6%Co) circular blades achieve 93 HRA hardness, outlasting HSS blades by 40% at 1,200m/min
- HIP-sintering ensures bending strength >3500MPa, preventing high-speed chipping
Case Study: CATL uses Φ200mm carbide circular blades to achieve 99.8% aluminum foil slitting yield
b. Separator Cutting Composite Blades
Style Combination:
- Circular+Straight Blade Composite:
- Upper: Φ50-100mm cemented carbide circular blade (DLC-coated)
- Lower: Cemented carbide straight blade (TiAlN-coated edge)
- Roll-cutting Process: 2-5° shear angle between blades reduces membrane stretching
Technical Parameters:
Blade Style | Separator Thickness | Cutting Speed | Burr Height |
---|---|---|---|
Diamond-coated circular | 10-50μm | 800m/min | ≤5μm |
Ceramic composite straight | 50-150μm | 500m/min | ≤10μm |
c. Bipolar Plate PCD Saw Blades
Innovative Design:
- Ultra-thin Saw Blades: 0.3-0.8mm thickness, 20-40TPI tooth density
- Tooth Structures:
- Alternate top bevel (ATB): For graphite-coated aluminum
- Flat tooth (FC): For titanium alloy bipolar plates
- Cooling Design: 0.1mm micro-cooling grooves between teeth, 30% better heat dissipation
Lifespan Comparison:
- Traditional carbide saw blades: >50μm wear after 500 cuts
- PCD saw blades: <10μm wear after 5,000 cuts (10x improvement)
d. Cell Dicing Ultra-thin Circular Blades
Extreme Design:
- Diameter: Φ30-80mm, thickness only 0.1-0.3mm
- Edge Treatment:
- Laser-finished to radius ≤2μm
- TiCN coating for enhanced wear resistance
- Dynamic Balance: G1 grade balance precision for 20,000rpm dicing
Applications:
- Prismatic cells: Φ50mm blade cuts aluminum casings with chipping ≤50μm
- Cylindrical cells: Φ30mm blade splits steel casings with verticality ≤0.01mm
e. Gasket Cutting Die Blades
Style Features:
- Punching Die Blades:
- Carbide punch (edge R0.05mm)
- HSS die (hard chrome-plated surface)
- Waterjet-assisted Blades:
- Tungsten carbide nozzle (0.1-0.3mm orifice)
- Combined with CNC 3-axis platform
Precision Metrics:
- Punching die: Gasket dimensions ±0.02mm
- Waterjet cutting: Complex curves ±0.05mm
3. Technical Breakthroughs in Cemented Carbide Blade Styles
a. Micron-level Control for Circular Blades
- Wheel Dressing Technology: W1.5 ultra-fine diamond wheel ensures edge straightness ±1μm/100mm
- Stress Relief Process: Vacuum annealing eliminates internal stress, keeping high-speed deformation <5μm
b. Tooth Innovation for Saw Blades
- Variable Pitch Design: 1.5-2.5mm gradient pitch suppresses cutting resonance
- Negative Rake Teeth: -5°~-10° rake angle enhances penetration into hard materials
c. Coating Adaptation to Blade Styles
Blade Style | Coating Type | Thickness | Friction Coefficient | Suitable Materials |
---|---|---|---|---|
Slitting circular | TiAlN | 2-3μm | 0.3-0.4 | Copper/aluminum foil |
PCD saw blade | DLC | 1-2μm | 0.1-0.2 | Graphite composites |
Separator straight | AlCrN | 3-5μm | 0.4-0.5 | Polypropylene separators |
4. Our Customized Blade Style Solutions
a. Style Development Process
- Condition Analysis: Acquire material thickness, cutting speed, equipment parameters
- 3D Modeling: Design 3D blade models (including edge curves and cooling channels)
- Simulation Verification: ANSYS simulation for stress distribution and thermal deformation
- Sample Prototyping: 5-axis machining for precise style manufacturing
b. Star Product Styles
- WC-10%Co Ultra-thin Circular Blade:
- Φ60mm diameter, 0.2mm thickness
- R0.03mm edge transition
- Suited for 15μm electrode slitting, burrs ≤3μm
- PCD Bipolar Plate Saw Blade:
- Φ150mm diameter, 0.5mm thickness
- 24TPI variable pitch design
- Increases graphite plate machining to 20 pieces/min
5. Blade Style Selection Guide
a. Style Selection by Material
- Copper/aluminum foil: Prioritize micro-serrated (6-50μm) or polished (50-200μm) circular blades
- Separator: Composite circular+straight blades (10-150μm)
- Bipolar plates: PCD saw blades (metal) or ceramic milling cutters (composites)
b. Style Selection by Efficiency
- High-volume production: Multi-blade circular systems (parallel cutting)
- Small-batch customization: Waterjet cutting (no mold costs)
Conclusion: Style Drives Productivity—Cemented Carbide Shapes Cutting Future
Every technological breakthrough in lithium battery manufacturing starts with blade style innovation. From micron-level circular blades to composite saw blades, [Kedel Carbide] leverages cemented carbide to provide end-to-end solutions from style design to mass production. Contact us today for customized blade style solutions, and let cutting precision become your core competitiveness!