Tape Slitter Blade
Tape slitting blades are specialized blades adapted to slitting machines, used to accurately slit various tape mother rolls into narrow-width finished products and ensure the quality of cut edges and dimensional precision.
Products Provided by Kedel
We offer the following types of blades. Whether you need standard sizes or customized sizes, we can precisely meet your unique requirements.
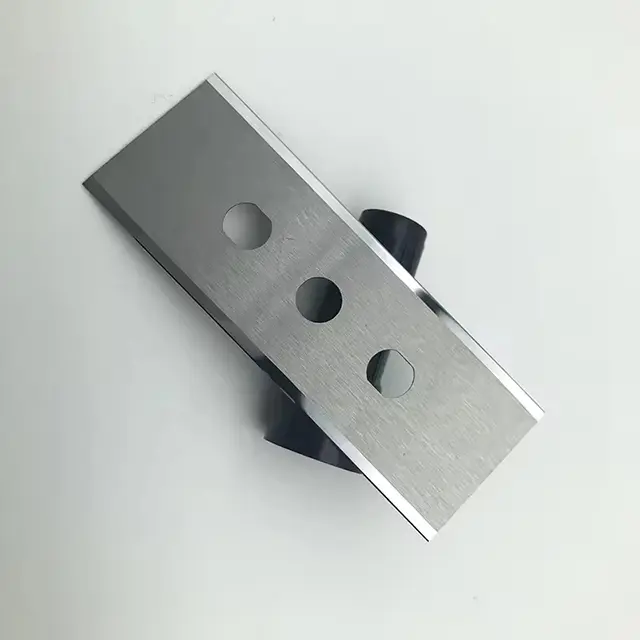
三孔直刀
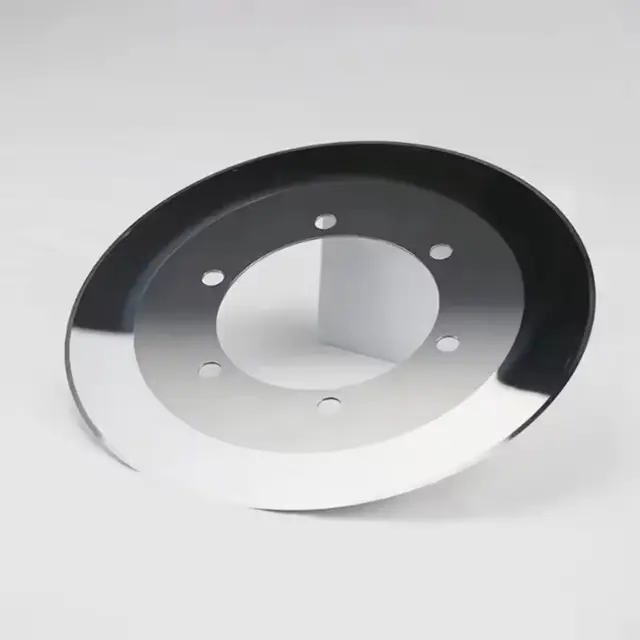
圆刀
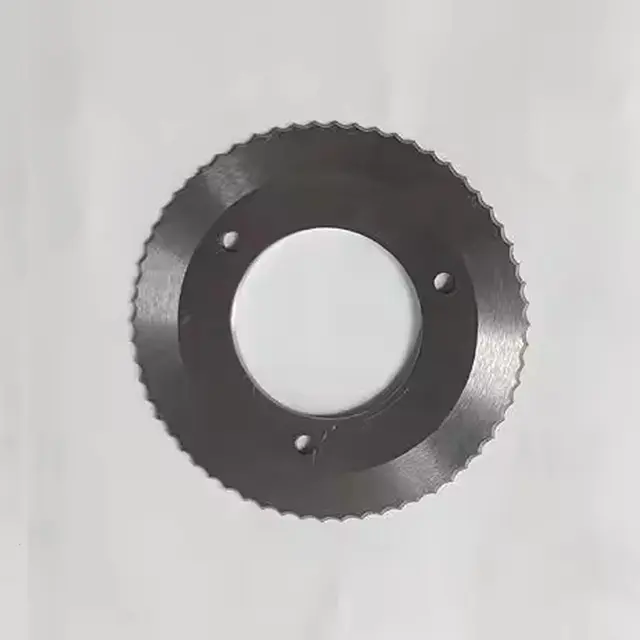
锯齿刀
Need custom blades? We design and make them
In view of the different properties of tapes such as BOPP carton – sealing tape and PET transparent tape, suitable cutting tools are matched for slitting to ensure cutting quality and efficiency and meet the demands of diverse production scenarios.

BOPP Carton Sealing Tape
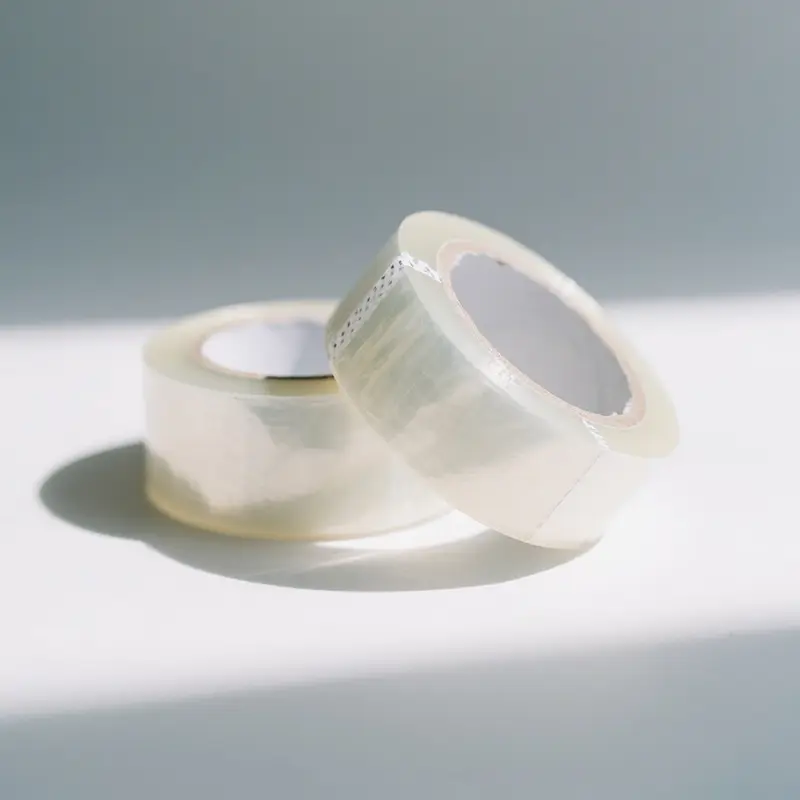
PET Transparent Tape
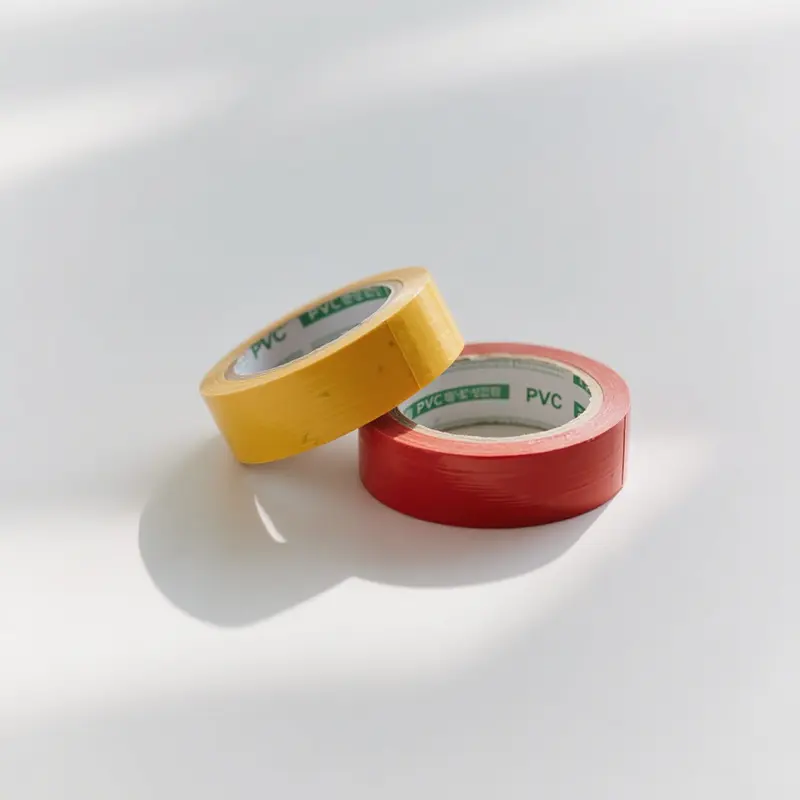
PVC Electrical Tape
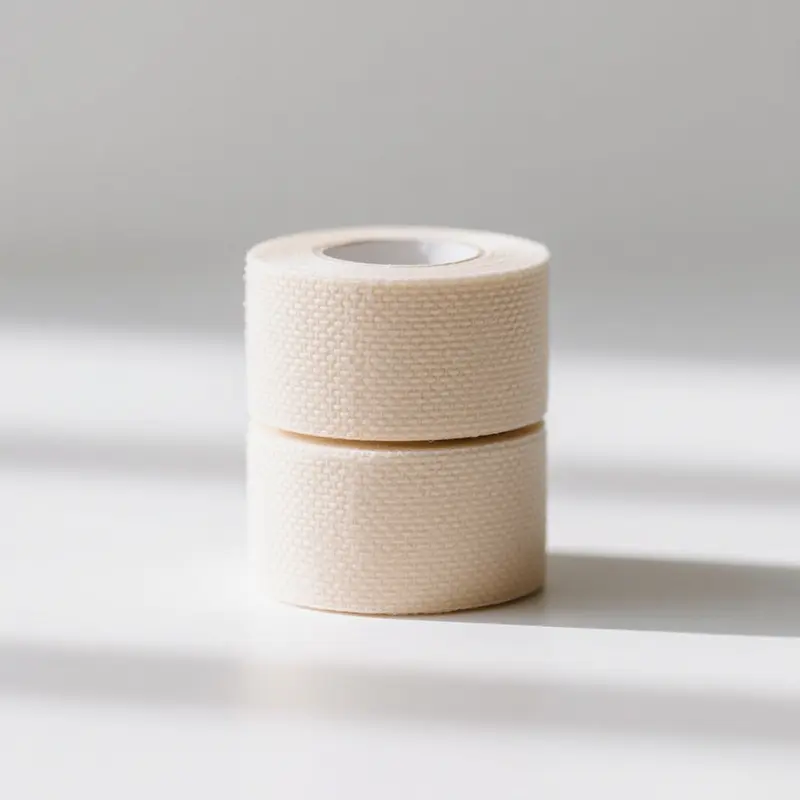
Medical Nonwoven Tape
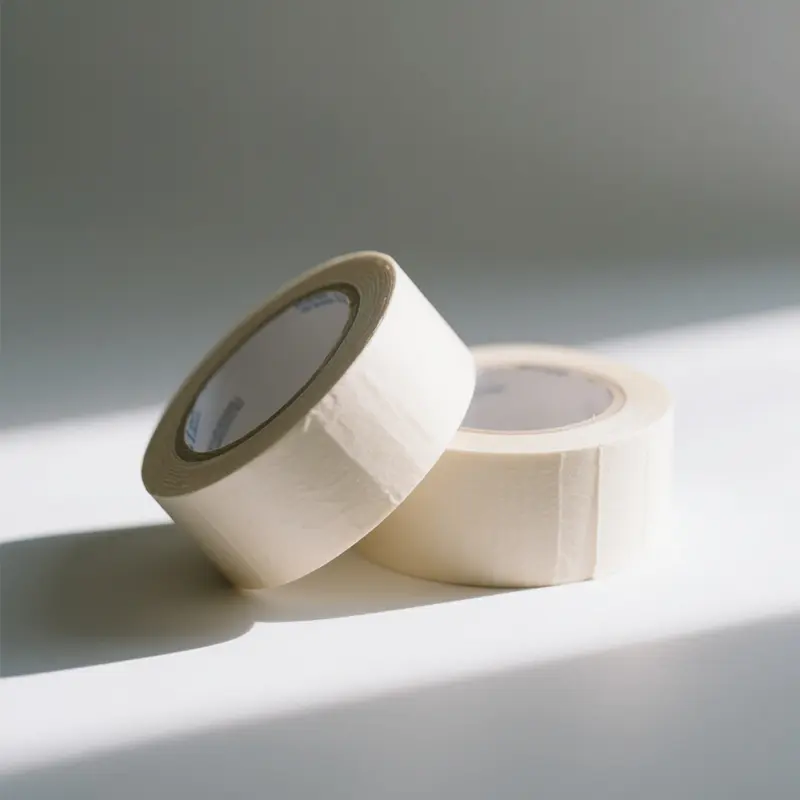
Masking Tape
Uncover Your Needs with Us!
If you have customization needs for tape slitting blades, please feel free to contact us! Please provide information such as the brand and model of the slitting equipment, the installation dimensions of the tool holder, the performance requirements of the blade (e.g., hardness, edge sharpness, wear resistance), and the actual working environment (e.g., tape material, production speed, cleanliness). Our engineers will customize an exclusive solution for you and communicate with you within 72 hours after receiving the information, helping you improve the efficiency and quality of tape slitting processing!
What is a Tape Slitter Blade?
Tape slitting blades are specialized tools designed to precisely cut large tape rolls into smaller ones with specified widths, and they are widely used in tape production across industries such as packaging, electronics, and medical fields. Classified by cutting characteristics, they include circular blades (high – speed and efficient, suitable for thick – film tapes like BOPP), flat blades (with excellent precision, ideal for thin tapes such as OCA), and serrated blades (which create easy – tear edges, commonly used for stationery tapes). Key parameters involve slitting accuracy (±0.05–0.1 mm), material properties (e.g., the wear resistance of tungsten carbide and the high hardness of ceramics), and the installation – compatible dimensions of the tool holder. Through stable cutting, these blades ensure smooth tape edges and uniform width, ultimately enhancing the production efficiency and quality of slit tapes.
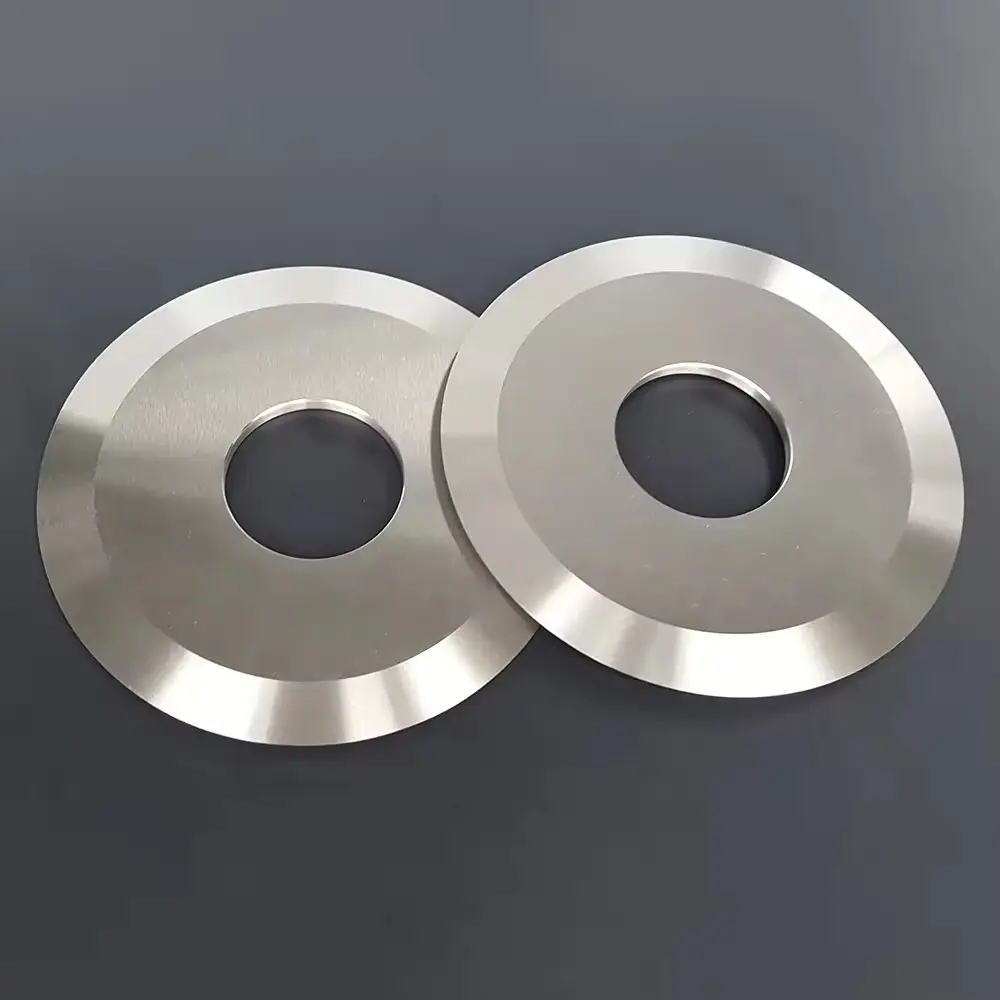
What are the common tool types used in Tape Slitter Blade ?
For tapes with different properties such as BOPP carton sealing tape and PET transparent tape, appropriate cutting tools are selected to ensure cutting quality and efficiency, meeting diverse production needs.
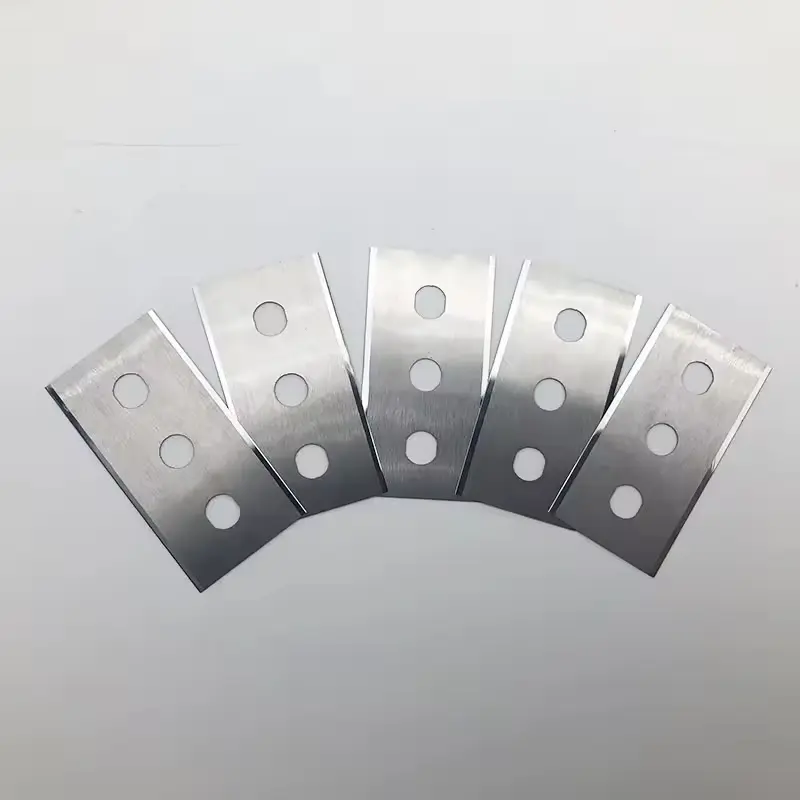
Three-Hole Straight Blade
Structural Features: Straight blade with three mounting holes, adapted for positioning and fixing in linear cutting stations.
Functional Advantages: Ensures straight cut edges, reduces stretching deformation during adhesive tape slitting, suitable for cutting high-viscosity and thin tapes.
Typical Applications: Slitting wide-format tape master rolls into narrow strips, clean-room slitting of medical tapes.
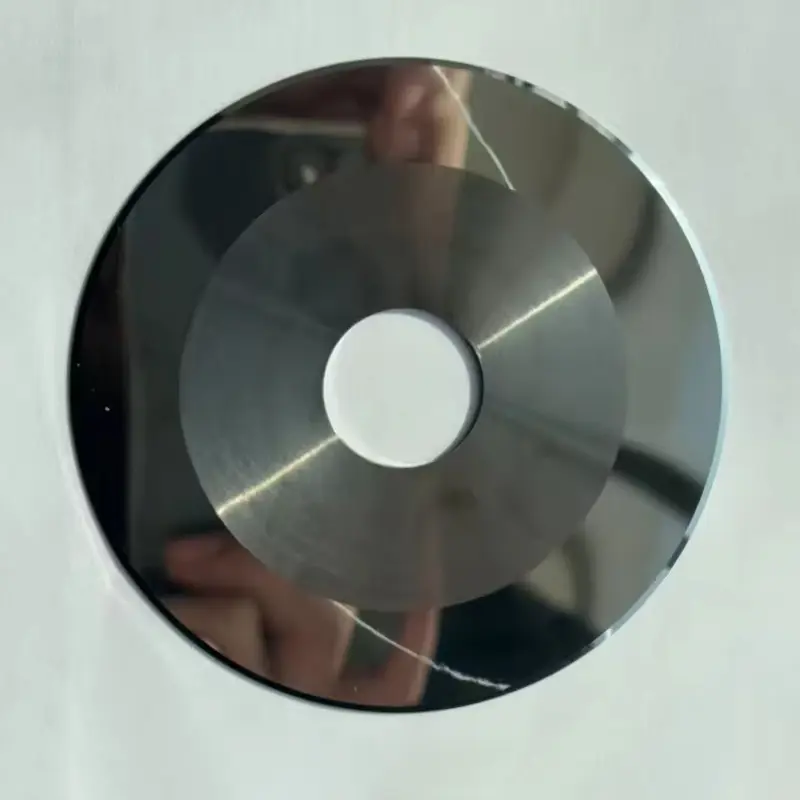
Rotary Blade (Disc Blade)
Structural Features: Circular structure with a central hole, meeting dynamic balance requirements for high-speed rotation.
Functional Advantages: Smooth cut edges at high speeds, reduces adhesion risk for high-viscosity tapes, improves slitting efficiency.
Typical Applications: On-line slitting in tape rewinding machines, cutting specified-length tape rolls on automatic cutting tables.
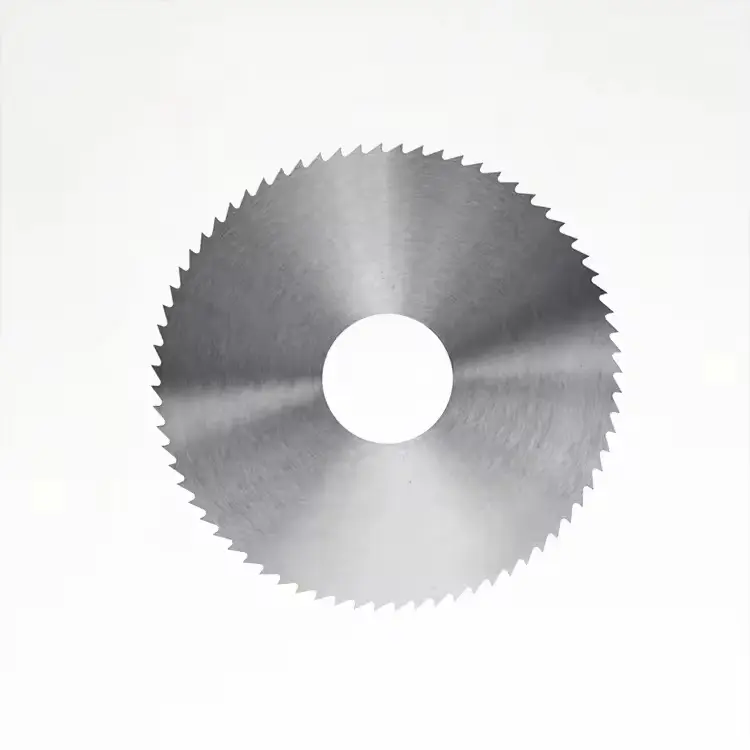
Serrated Blade
Structural Features: Blade edge in regular serrated shape, tooth profile matched to tape fiber characteristics.
Functional Advantages: Combines cutting and chip evacuation, tackles challenges in thick tape slitting, reduces adhesive residue.
Typical Applications: Slitting thick foam and cloth-based tapes, pre-slitting in 异形 (special-shaped) tape die-cutting processes.
What materials can be used to make cutting blades?
The use of different materials in manufacturing tape slitting blades aims to address the differences in tape material, thickness, and production scenarios, achieving optimal balance among wear resistance, cutting precision, production efficiency, and cost.
1. Cemented Carbide (Tungsten Steel)
- Core Advantage: High wear resistance (cost-effective), reusable via resharpening.
- Suited Tapes: BOPP packing tapes, PET medium-thick films (30-100μm thickness).
- Application: Mass slitting of logistics tapes and general electronic tapes.
2. Alumina Ceramic
- Core Advantage: High-speed slitting (ideal for high-volume production lines), heat-resistant to prevent adhesive buildup.
- Suited Tapes: Thick foam tapes, wear-resistant filled tapes (>100μm thickness).
- Application: Large-scale production (up to millions of meters daily).
3. Silicon Nitride Ceramic
- Core Advantage: High toughness and impact resistance, minimizing deformation of elastic tapes during slitting.
- Suited Tapes: Silicone tapes, foam tapes, or multi-layer composite tapes.
- Application: Slitting of tapes requiring both strength and flexibility.
4. Diamond-Coated Blades
- Core Advantage: Ultra-fine cutting edge, minimal burrs, suitable for ultra-thin tapes.
- Suited Tapes: Optical films (OCA), lithium battery protective tapes (≤30μm thickness).
- Application: Precision slitting for electronic and semiconductor tapes.
5. High-Speed Steel (HSS)
- Core Advantage: Good toughness, low processing cost, but shorter lifespan.
- Suited Tapes: Stationery tapes, ordinary paper-based tapes (≤20μm thickness).
- Application: Small-batch trials, laboratory slitting, or low-cost needs.
6. Coating Enhancement Technologies (TiN/TiAlN, etc.)
- Core Advantage: Improves wear resistance and anti-adhesion, optimizing slitting performance.
- Suited Tapes: General performance upgrades for various tapes (e.g., PVC tapes).
- Application: Cost-optimized solutions for non-critical materials.
Simple Selection Logic:
- By thickness: Ultra-thin (≤30μm) → diamond coating; medium (30-100μm) → cemented carbide; thick (>100μm) → ceramic.
- By material: Elastic/high-adhesion tapes → silicon nitride ceramic or diamond coating; ordinary tapes → cemented carbide or HSS.
The significance of understanding these parameters lies in precisely matching blade performance based on tape characteristics and usage scenarios to achieve the optimal balance among cutting efficiency, cost control, and blade lifespan.
Purchase Parameters
- Material Type
- Determines wear resistance, toughness, and suitability for specific tape materials (e.g., tungsten steel for general tapes, diamond coating for ultra-thin films).
- Hardness (HRC/HV)
- Directly affects blade lifespan; higher hardness (e.g., ceramic >60 HRC) suits abrasive tapes but may be brittle.
- Edge Precision
- Tolerance (e.g., ±0.01mm) and surface roughness (Ra value) impact cutting burrs and tape edge quality.
- Blade Geometry
- Angle (e.g., clearance angle, rake angle) and thickness, optimized for tape thickness (e.g., thinner blades for <30μm tapes).
- Coating Properties
- If coated (TiN/TiAlN), check adhesion strength and anti-stick performance for high-speed slitting.
Usage Parameters
- Cutting Speed & Rotation Speed
- Matched to blade material (e.g., ceramic blades allow 200-500 m/min, while HSS requires ≤100 m/min to avoid overheating).
- Slitting Pressure
- Adjusted by tape thickness (e.g., 5-10N for thin films, 15-30N for thick foam) to prevent deformation or blade damage.
- Temperature Control
- Critical for ceramic/diamond blades (≤120°C) to maintain edge integrity; cooling systems may be needed.
- Blade Life Cycle
- Expected service life (e.g., tungsten steel can be resharpened 5-8 times, ceramic 2-3 times) and replacement intervals.
- Tape Compatibility
- Ensure the blade’s wear resistance matches tape adhesiveness (e.g., high-tack tapes require anti-stick coatings).
Core Logic
- Purchase: Align material/hardness with tape specifications to balance cost and performance.
- Usage: Optimize speed/pressure based on blade properties to prevent premature wear or cutting defects.
The significance of maintaining these tools lies in using scientific and standardized measures (cleaning, grinding, protection, etc.) to achieve a comprehensive optimization and long-term balance among tool service life, cutting precision, and operating costs.
1. Daily Cleaning & Debris Removal
- Immediate post-use cleaning: Wipe the blade edge with alcohol or a non-corrosive solvent to remove adhesive residues, dust, or tape debris (high-tack tapes demand prompt cleaning to avoid coating failure).
- Ultrasonic cleaning: For stubborn stains, use neutral detergent with an ultrasonic cleaner (avoid alkaline solutions for ceramic/diamond coatings).
2. Edge Protection & Storage
- Anti-impact storage: Place blades in foam-lined cases or plastic sleeves to prevent edge chipping (ceramic blades are highly impact-sensitive).
- Humidity control: Store in a dry environment (relative humidity ≤40%) with desiccants to prevent steel blade rust; for long-term storage, apply anti-rust oil to tungsten carbide blades.
3. Edge Grinding & Repair
- Regular regrinding intervals: Set cycles based on material properties (e.g., 500–1000 hours for tungsten carbide, 200–300 hours for ceramics), using a diamond grinding wheel for precision.
- Edge inspection: Check for micro-cracks or burrs under a microscope; replace immediately if chipping exceeds 0.05mm (ceramic blades risk fracture).
4. Coating Maintenance
- Avoid abrasive cleaning: For coated blades (TiN/TiAlN), use a soft-bristle brush instead of wire brushes to preserve anti-adhesive and wear-resistant properties.
- Recoating when needed: If coating peeling occurs (e.g., white spots on TiN), recoat promptly (costs ~30% of a new blade).
5. Operational Precautions
- Temperature management: Ensure cooling systems (air/liquid cooling) keep blade temperature ≤120℃ during high-speed slitting (prevent thermal softening of high-speed steel or coating detachment).
- Proper mounting: Tighten blades evenly to avoid eccentric rotation (causing uneven wear); use dynamic balancing equipment for high-speed applications.
6. Preventive Maintenance Schedule
Item | Frequency | Key Actions |
---|---|---|
Microscopic edge check | Every 50 production runs | Inspect wear patterns with a 50× magnifier; record surface roughness (Ra value) changes. |
Coating integrity test | Monthly | Perform tape adhesion testing per ASTM D3359 to detect early peeling. |
Equipment alignment | Quarterly | Ensure slitting shaft runout ≤0.02mm to avoid blade stress concentration. |
Core Principle
The significance of scientifically setting tool replacement cycles lies in achieving dynamic balance among tool performance (precision/efficiency), usage costs (wear/maintenance), and production safety (failure risks) by quantifying wear thresholds, thereby preventing quality degradation or equipment damage caused by excessive wear.
Tool Replacement Cycles for Tape-Cutting Blades (By Material)
Tool Material | Applicable Tapes | Reference Replacement Cycle | Key Factors | Replacement Warnings |
---|---|---|---|---|
Tungsten Carbide | General transparent/BOPP/sealing tape | 500–800 hrs (80,000–100,000 cuts) | Tape tack (high-tack shortens cycle by 20%) | Continuous burrs, increased adhesive residue |
Ceramic (Zirconia) | Medical-grade/optically clear tape | 200–400 hrs (50,000–60,000 cuts) | Blade temp (≤120℃), impact load | Edge chipping >0.03mm, reduced light transmittance |
Diamond-Coated (PCD) | High-tack foam/electronic tape | 800–1200 hrs (120,000–150,000 cuts) | Coating anti-adhesion, cleaning frequency | Local coating peeling, tape sticking |
TiC-Coated (Titanium Carbide) | Aluminum foil/high-temp tape | 400–600 hrs (60,000–80,000 cuts) | Coating stability in high temps | Coating discoloration, carbonized cut edges |
Supplementary Guidelines
- Cycle Adjustments: For ultra-tacky tapes (e.g., acrylic), reduce cycles by 30%; daily ultrasonic cleaning extends life by 15%–20%.
- Precision Scenarios: In electronics (e.g., tapes <0.1mm), replace at the lower cycle limit to avoid ±0.05mm dimensional errors.